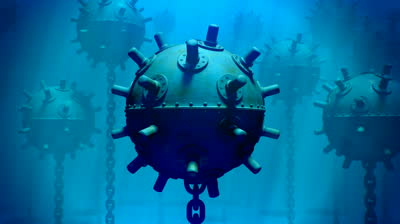
Like
a spider's web, mines lay in wait for unwary ships and submarines

NATO
AUTONOMOUS MINE SWEEPERS, OCTOBER 2014
From September 22 to October 13, 2014, the
NATO Research Vessel Alliance is conducting the Multinational AutoNomy Experiment (MANEX ‘14) along the Ligurian coast to demonstrate the advantages of mapping the seabed using autonomous vehicles.
Throughout the experiment, multiple autonomous underwater vehicles (AUVs) equipped with modern sensors relevant to
NATO minehunting missions are being employed in the Ligurian Sea along the
Italian coast between Framura and Bonassola to collect data that will allow NATO researchers to advance the area of seabed mapping using autonomous vehicles, mainly for mine countermeasures applications. Improved capabilities in seabed mapping can also lead to positive advancements in other fields such as support for environmental and
archeological surveys.
Onboard the NATO Research Vessel Alliance, operated by the NATO Centre for Maritime Research and Experimentation (CMRE), part of the
NATO Science and Technology Organization, scientists and engineers from eight institutions and ten nations are exercising state-of-the-art high resolution underwater acoustic imaging systems and autonomous vehicle behaviors. The use of robots improves safety by removing the need for navy personnel to operate in a potentially dangerous area like a minefield.
CMRE has a world-leading expertise in
autonomous mine countermeasures and seabed mapping. For many years, the center has worked to transform the way mine countermeasures are conducted, from a post-Cold War approach that focuses on post-operations clearance using
surface
ships, to a quickly deployable, autonomous system-of-systems that is scalable, cost effective, and minimizes risk to personnel. This includes developing techniques for handling the large data rates associated with modern high-resolution
sonar, and developing AUV systems that can make adjustments to pre-planned routes based on data that are gathered in situ.
During MANEX ‘14, CMRE capabilities, AUVs and sensors will be challenged in a very complex environment where the sea bottom characteristics vary over the range of flat sand, seabed ripples and heavy clutter. In particular, so-called Automatic Target Recognition (ATR) algorithms,
computer programs used to find and identify underwater objects in sonar imagery, will be stressed in such a high clutter and complex environment with the objective of maximizing detection rates whilst minimizing false alarms. The data collected will greatly help to enhance the quality of the scientific research conducted by the Alliance in this field. Overall, the multinational aspect of the MANEX ‘14 trial will also allow NATO and Nations to gain experience in how autonomous systems can be used in joint mine countermeasures missions.
The MANEX ’14 sea trial is funded by the Allied Command Transformation (ACT).
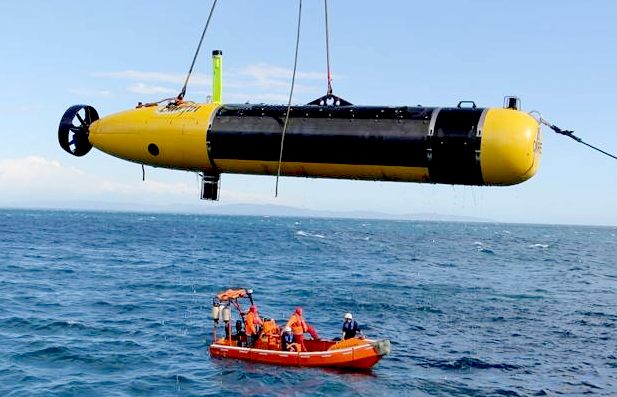
NATO's
MANEX experiment. Mines are an inevitable consequence of an unstable
world. Legitimate use of mines includes protecting sovereign waters from
covert operations that might be illegal in international law. In times of
war, supply routes may be mined to cripple an enemies war efforts. The
above method of deploying mine is crude and potentially still risky to the
human operators.
US
NAVY, JANUARY 2013
The US Navy's next wave of robots will take on one of the most dangerous missions on the open water: destroying mines.
Anti-mine warfare is a critical mission for the US
Navy, as nations like Iran can disrupt the global economy by threatening to plant mines in crucial commercial waterways. But the tools that the US Navy has to disable mines have a crucial weakness: they depend on humans getting too close to them for comfort. When it comes to blowing up, or "sweeping" mines, explains Duane Ashton, "There's a saying: 'Hunt if you can, sweep if you must.'"
Ashton, the US Navy's programme manager for its seafaring robots, has a different idea: let the robots do the dirty work. By April, he tells Wired, he hopes to solicit defence contractors to build something called the Unmanned Influence Sweep System, or UISS, a
robotic ship charged with speeding out into suspected minefields and essentially fooling them into detonating them before they come in contact with a ship full of sailors. If the UISS works as intended, it'll be part of a fleet of near-future US Navy
robot ships and subs designed to neutralise some of the most immediate threats on the high seas.
The idea is to launch the UISS from a Littoral Combat Ship, the new close-to-shore fighter that the
US Navy wants to be the mine-stopper of the future, among its other missions. Currently, minesweeping is a task for manned ships and helicopters like the Avenger-class mine
countermeasures ship and the MH-53 helo. "This would be the first unmanned sweep system [for a] surface capability," Ashton says, something "a lot of countries are looking at" but none have yet succeeded in developing. It works by playing a kind of practical joke on a minefield.
Underwater mines don't necessarily need to detonate on contact with a ship. Many explode when they sense the acoustic sounds that ships give off when passing through a waterway, or by detecting the magnetic signatures of the metals used to construct ships. So the UISS spoofs those acoustic and magnetic signals, getting the mines to "wake up," in Ashton's phrase
- that is, detonate - well out of range of a Littoral Combat Ship or other US Navy ship charged with keeping waterways mine-free. In 2011, testing in the
Florida waters with a 12-metre, remote-controlled UISS prototype proved that the robot's joke could get the mines to explode far from any sailor. Last week, in a much-anticipated step ahead of the UISS solicitation, the US Navy asked defence companies for their feedback on constructing the robot minesweeper.
There's long been concern about the ability of the new Littoral Combat Ship, whose missions include stopping mines, to accurately spot mines. Last year, the Pentagon's top weapons tester judged that the sensor and laser systems designed for the Littoral Combat Ship were " deficient" for their major mine-spotting task. And there's little margin for error: Mines are likely to blow the Littoral Combat Ship to bits if the UISS can't stop them.
But since the Littoral Combat Ship is designed to be modular - that is, to swap out its sensor packages when better ones come on-line
- the US Navy's response is to let the robots take care of hunting and sweeping mines. In April, it unveiled the Knifefish, an experimental, oblong underwater robot launched from a Littoral Combat Ship designed to hunt mines.
But the Knifefish can only find the mines. It can't destroy them. That's where the US Navy wants the UISS to come in. In principle, a controller aboard a Littoral Combat Ship will program the UISS out to steam out to a set of coordinates, possibly provided by the Knifefish, and from there it'll emit its spoof signals prompting the mines to detonate, and then swim back on its own to its mothership, which can rest easier knowing it won't be steaming into a minefield. Ultimately, the Navy wants 52 of the robots, including training modules, so that every Littoral Combat Ship tasked with stopping mines carries a UISS.
The UISS and the Knifefish are part of a relatively new trend in naval robotics: unmanned ships and subs that can perform some of the Navy's most pressing and most dangerous missions. There's also the ACTUV, a project from the Pentagon futurists at
Darpa, in which a semi-autonomous ship detects and hunts enemy submarines
- another high-stakes mission that counters one of the Navy's most immediate threats. Previous Navy robotics projects have either taken to the skies, like with carrier-based drones or cargo helicopters, or focused on more peripheral jobs like putting out shipboard fires or even exploring space. There have been some sound technological reasons for this, like the tough propulsion and fuelling challenges implicit in long-range robotic travel. But these newer programs point to increased Navy trust in robots to meet some of its most central maritime challenges.
The specifics of the UISS are still undecided. That'll be a job for Ashton and the Navy to work out with an industry excited for the robo-sweeper contract. (The AAI Corporation, for instance, hopes its Common Unmanned Surface Vessel will become the basis for the UISS.) The current plan is to get the UISS out into the fleet by 2017. If Ashton can pull that off, adversaries might have cause to flip the Navy's adage: Mine if you must.
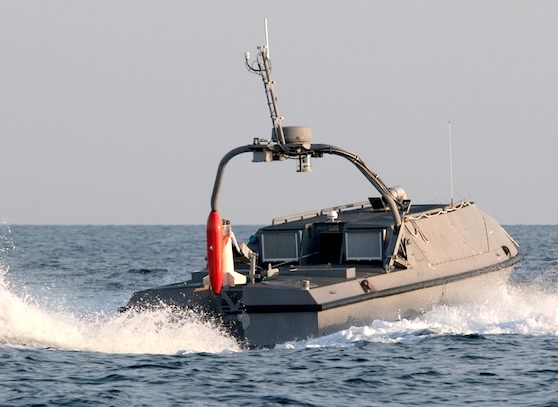
DESCRIPTION
A naval mine is a self-contained explosive device placed in water to destroy surface ships or submarines. Unlike depth charges, mines are deposited and left to wait until they are triggered by the approach of, or contact with, an enemy vessel. Naval mines can be used offensively
- to hamper enemy shipping movements or lock vessels into a harbour; or defensively
- to protect friendly vessels and create "safe" zones.
Mines can be laid in many ways: by purpose-built minelayers, refitted ships, submarines, or aircraft—and even by dropping them into a harbour by hand. They can be inexpensive: some variants can cost as little as US$1000, though more sophisticated mines can cost millions of
dollars, be equipped with several kinds of sensors, and deliver a warhead by rocket or
torpedo.
Their flexibility and cost-effectiveness make mines attractive to the less powerful belligerent in asymmetric warfare. The cost of producing and laying a mine is usually anywhere from 0.5% to 10% of the cost of removing it, and it can take up to 200 times as long to clear a minefield as to lay it. Parts of some World War II naval minefields still exist because they are too extensive and expensive to clear. It is possible for some of these 1940s-era mines to remain dangerous for many years to come.
Mines have been employed as offensive or defensive weapons in rivers, lakes, estuaries, seas, and oceans, but they can also be used as tools of psychological warfare. Offensive mines are placed in enemy waters, outside
harbours and across important shipping routes with the aim of sinking both merchant and military vessels. Defensive minefields safeguard key stretches of coast from enemy ships and submarines, forcing them into more easily defended areas, or keeping them away from sensitive ones.
Minefields designed for psychological effect are usually placed on trade routes and are used to stop shipping reaching an enemy nation. They are often spread thinly, to create an impression of minefields existing across large areas. A single mine inserted strategically on a shipping route can stop maritime movements for days while the entire area is swept.
International law requires nations to declare when they mine an area, in order to make it easier for civil shipping to avoid the mines. The warnings do not have to be specific; for example, during World War II, Britain declared simply that it had mined the English Channel, North Sea, and French coast.
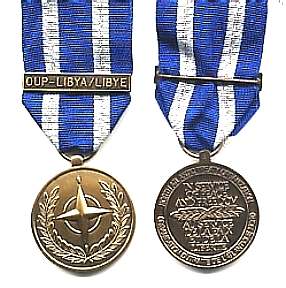
NATO
- Libya mine disposal awards
TYPES
OF MINES
CONTACT
The earliest mines were usually of this type. They are still used today, as they are extremely low cost compared to any other anti-ship weapon and are effective, both as a terror weapon and to sink enemy ships. Contact mines need to be touched by the target before they detonate, limiting the damage to the direct effects of the explosion and usually affecting only the single vessel that triggers them.
Early mines had mechanical mechanisms to detonate them, but these were superseded in the 1870s by the Hertz Horn (or chemical horn), which was found to work reliably even after the mine had been in the sea for several years. The mine's upper half is studded with hollow lead protuberances, each containing a glass vial filled with sulfuric acid. When a ship's hull crushes the metal horn, it cracks the vial inside it, allowing the acid to run down a tube and into a lead-acid battery which until then contains no acid electrolyte. This energizes the battery, which detonates the explosive.
Earlier forms of the detonator employed a vial of sulfuric acid surrounded by a mixture of potassium perchlorate and sugar. When the vial was crushed, the acid ignited the perchlorate / sugar mix, and the resulting flame ignited the gunpowder charge.
During the initial period of World War
I, the British Navy used contact mines in the English Channel and later in large areas of the North Sea to hinder patrols by
German
submarines. Later, the American antenna mine was widely used because submarines could be at any depth from the surface to the seabed. This type of mine had a copper wire attached to a buoy that floated above the explosive charge which was weighted to the seabed with a
steel cable. If a submarine's steel hull touched the copper wire, the slight voltage change caused by contact between two dissimilar metals was amplified and detonated the explosives.
LIMPET
Limpet mines are a special form of contact mine that are manually attached to the target by magnets and left, and are so named because of the superficial similarity to the limpet, a mollusk.
MOORED
CONTACT MINES
Generally, this mine type is set to float just below the surface of the
water or as deep as five meters. A steel cable connecting the mine to an anchor on the seabed prevents it from drifting away. The explosive and detonating mechanism is contained in a buoyant metal or plastic shell. The depth below the surface at which the mine floats can be set so that only deep draft vessels such as aircraft carriers, battleships or large cargo ships are at risk, saving the mine from being used on a less valuable target. In littoral waters it is important to ensure that the mine does not become visible when the sea level falls at low tide, so the cable length is adjusted to take account of tides. Even during the Second World War, there were mines that could be moored in 300m-deep water (Example: The U.S. Mark 6).
Floating mines typically have a mass of around 200 kg, including 80 kg of explosives e.g.
TNT, minol or
amatol.
During WWII mine traps were used for blocking port entrances. Two floating mines were anchored some distance apart on either side of a shipping channel, linked by a chain. When a deep draft vessel passed through the trap it would pull the chain along with it, dragging the mines onto the sides of the ship; the resulting double explosion often sank it. This system was not used extensively, but proved effective in blocking ports.
DRIFTING
CONTACT MINES
Drifting mines were occasionally used during World War I and World War II. However, they were more feared than effective. Sometimes floating mines break from their moorings and become drifting mines; modern mines are designed to deactivate in this event. After several years at sea, the deactivation mechanism might not function as intended and the mines may remain live. Admiral Jellicoe's British fleet did not pursue and destroy the outnumbered
German High Seas Fleet when it turned away at the Battle of Jutland because he thought they were leading him into a trap: he believed it possible that the Germans were either leaving floating mines in their wake, or were drawing him towards submarines, although neither of these was the case.
Churchill promoted "Operation Royal Marine" in 1940 and again in 1944 where floating mines were put into the Rhine in France to float down the river, becoming active after a time calculated to be long enough to reach German territory.
After World War I the drifting contact mine was banned, but was occasionally used during World War II. The drifting mines were much harder to remove than tethered mines after the war, and they caused about the same damage to both sides.
BOTTOM
CONTACT MINES
A bottom contact mine is the simplest form of mine. It is merely an explosive charge with some form of
fuse fitted lying on the seafloor. They have been used against submarines, as submarines sometimes lie on the seafloor to reduce their acoustic signature. They are also used to prevent landing craft from reaching the shore and were a major obstacle during the D-Day landings. The Germans used antitank mines here with minor modifications to make them more reliable underwater, attaching the mines to the front of many of the obstacles seen in photos of the landing.
These mines usually weighed 2 to 50 kg, including 1 to 40 kg of explosives (TNT or hexatonal).
REMOTELY
CONTROLLED MINES
Frequently used in combination with coastal artillery and hydrophones, controlled mines (or command detonation mines) can be in place in peacetime, which is a huge advantage in blocking important shipping routes. The mines can usually be turned into "normal" mines with a switch (which prevents the enemy from simply capturing the controlling station and deactivating the mines), detonated on a signal or be allowed to detonate on their own. The earliest ones were developed around 1812 by Robert Fulton. The first remotely controlled mines were moored mines used in the
American Civil
War, detonated electrically from shore. They were considered superior to contact mines because they did not put friendly shipping at risk.
INFLUENCE
MINES
These mines are triggered by the influence of a ship or submarine, rather than direct contact. Such mines incorporate electronic sensors designed to detect the presence of a vessel and detonate when it comes within the blast range of the warhead. The
fuses on such mines may incorporate one or more of the following sensors: magnetic, passive acoustic or water pressure displacement caused by the proximity of a vessel.
First used during the First World War, their use became more general in the
Second World
War. The sophistication of influence mine
fuses has increased considerably over the years as first transistors and then microprocessors have been incorporated into designs. Simple magnetic sensors have been superseded by total-field magnetometers. Whereas early
magnetic mine
fuses would respond only to changes in a single component of a target vessel's magnetic field, a total field magnetometer responds to changes in the magnitude of the total background field (thus enabling it to better detect even degaussed ships). Similarly, the original broadband hydrophones of 1940s acoustic mines (which operate on the integrated volume of all frequencies) have been replaced by narrow-band sensors which are much more sensitive and selective. Mines can now be programmed to listen for highly specific acoustic signatures (e.g. a gas turbine powerplant and/or cavitation sounds from a particular design of propeller) and ignore all others. The sophistication of modern electronic mine
fuses incorporating these Digital Signal Processing capabilities makes it much more difficult to detonate the mine with electronic countermeasures because several sensors working together (e.g. magnetic, passive acoustic and water pressure) allow it to ignore signals which are not recognised as being the unique signature of an intended target vessel.
Modern influence mines such as the BAE Stonefish are computerised, with all the programmability that this implies e.g. the ability to quickly load new acoustic signatures into
fuses, or program them to detect a single, highly distinctive target signature. In this way, a mine with a passive acoustic
fuse can be programmed to ignore all friendly vessels and small enemy vessels, only detonating when a very large enemy target passes over it. Alternatively, the mine can be programmed specifically to ignore all surface vessels regardless of size and exclusively target submarines.
Even as far back as the Second World War it was possible to incorporate a "ship counter" facility into mine
fuses e.g. set the mine to ignore the first two ships to pass over it (which could be mine-sweepers deliberately trying to trigger mines) but detonate when the third ship passes overhead—which could be a high-value target such as an aircraft carrier or oil tanker. Even though modern mines are generally powered by a long life lithium battery, it is important to conserve power because they may need to remain active for months or even years. For this reason, most influence mines are designed to remain in a semi-dormant state until an unpowered (e.g. deflection of a mu-metal needle) or low-powered sensor detects the possible presence of a vessel, at which point the mine
fuse powers up fully and the passive acoustic sensors will begin to operate for some minutes. It is possible to program computerised mines to delay activation for days or weeks after being laid; similarly, they can be programmed to self-destruct or render themselves safe after a preset period of time, e.g., 12 days or 12 months. Generally, the more sophisticated the mine design, the more likely it is to have some form of anti-handling device fitted in order to hinder clearance by divers or remotely piloted submersibles.
MOORED
MINES
The moored mine is the backbone of modern mine systems. They are deployed where water is too deep for bottom mines. They can use several kinds of instruments to detect an enemy, usually a combination of acoustic, magnetic and pressure sensors, or more sophisticated optical shadows or electro potential sensors. These cost many times more than contact mines. Moored mines are effective against most kinds of ships. As they are cheaper than other anti-ship weapons they can be deployed in large numbers, making them useful area denial or
"channelizing" weapons. Moored mines usually have lifetimes of more than 10 years, and some almost unlimited. These mines usually weigh 200 kg (440 lb), including 80 kg (175 lb) of explosives (hexatonal). In excess of 150 kg (330 lb) of explosives the mine becomes inefficient, as it becomes too large to handle and the extra explosives add little to the mine's effectiveness.
BOTTOM
MINES
Bottom mines are used when the water is no more than 60 meters (180 ft) deep or when mining for submarines down to around 200 meters (660 ft). They are much harder to detect and sweep, and can carry a much larger warhead than a moored mine. Bottom mines commonly utilize multiple types of sensors, which are less sensitive to sweeping.
These mines usually weigh between 150 and 1,500 kilograms (330 to 3,300 pounds), including between 125 and 1,400 kg (275 to 3,090 pounds) of explosives.
ANTI
SWEEP MINE
The anti sweep mine is a very small mine (40 kg warhead) with as small a floating device as possible. When the wire of a mine sweep hits the mine, it "sinks", letting the sweep wire drag along the anchoring wire of the mine until the sweep hits the mine. That detonates the mine and cuts the sweeping wire. They are very cheap and usually used in combination with other mines in a minefield to make sweeping more difficult. One type is the Mark 23 used by the
United States during World War II.
TORPEDO
MINE
The
torpedo mine is a self-propelled variety, able to lie in wait for a target and then pursue it e.g. the Mark 60 CAPTOR. Other designs such as the Mk 67 Submarine Launched Mobile Mine (which is based on a Mark 37 torpedo) are capable of swimming as far as 10 miles through or into a channel, harbor, shallow water area and other zones which would normally be inaccessible to craft laying the device. After reaching the target area they sink to the sea bed and act like conventionally laid influence mines. Generally, torpedo mines incorporate computerised acoustic and magnetic fuzes.
The U.S. Mark 24 "mine", code-named FIDO, was actually an ASW homing torpedo. The mine designation was disinformation to conceal its function.
NUCLEAR
MINE
During the Cold War a test was conducted with naval mine fitted with tactical nuclear warheads for the "Baker" shot of Operation Crossroads. This weapon was experimental and never went into production. There have been some reports that North Korea may be developing a nuclear mine. The Seabed Arms Control Treaty prevents the placement of nuclear weapons on the seabed beyond a 12-mile coast zone.
DUMMY
MINES
Plastic drums filled with sand or concrete are periodically rolled off the side of ships as real mines are laid in large mine-fields. These inexpensive false targets (designed to be of a similar shape and size as genuine mines) are intended to slow down the process of mine clearance: a mine-hunter is forced to investigate each suspicious sonar contact on the sea bed, whether it is real or not. Often a maker of Naval mines will provide both training and dummy versions of their mines.
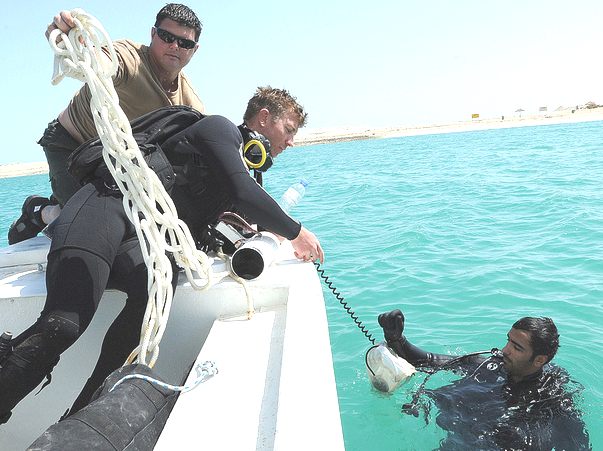
MINE
LAYING
Historically several methods were used to lay mines. During the First and Second World Wars, the Germans used U-boats to lay mines around the UK. In the Second World War, aircraft came into favour for mine laying with the one of largest such examples being the mining of the Japanese sea routes in Operation Starvation.
Laying a minefield is a relatively fast process with specialized ships, which is still today the most common method. These minelayers can carry several thousand mines and manoeuvre with high precision. The mines are dropped at a predefined interval into the water behind the ship. Each mine is recorded for later clearing, but it is not unusual for these recordings to be lost together with the ships. Therefore many countries demand that all mining operations shall be planned on land and records kept so the mines can later be recovered more easily.
Other methods to lay minefields include:
* Converted merchant ships – rolled or slid down ramps
* Aircraft – descent to the water is slowed by a parachute
* Submarines – launched from torpedo tubes or deployed from specialized mine racks on the sides of the
submarine
* Combat boats – rolled off the side of the boat
* Camouflaged boats – masquerading as fishing boats
* Dropping from the shore – typically smaller, shallow-water mines
* Attack divers – smaller shallow-water mines
In some cases, mines are automatically activated upon contact with the water. In others, a safety lanyard is pulled (e.g. one end attached to the rail of a ship, aircraft or
torpedo tube) which starts an automatic timer countdown before the arming process is complete. Typically, the automatic safety-arming process takes some minutes to complete. This is in order to give the people laying the mines sufficient time to move out of its activation/blast zone.
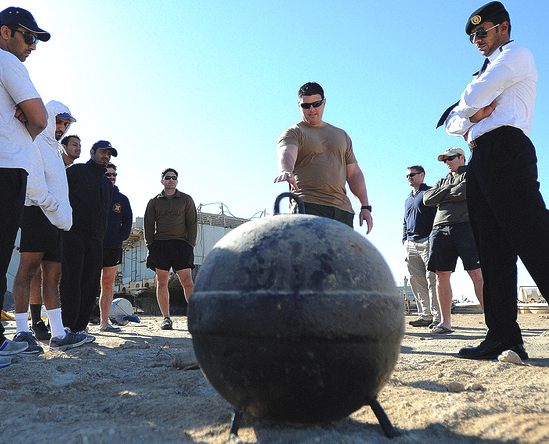
CLEARING
WWII MINES
Between 600,000 and 1,000,000 naval mines of all types were laid in
World War II. Advancing military forces worked to clear mines from newly taken areas, but extensive minefields remained in place after the war. Air-dropped mines had an additional problem for mine sweeping operations: they were not meticulously charted. In
Japan, much of the B-29 mine-laying work had been performed at high altitude, with the drifting on the wind of mines carried by parachute adding a randomizing factor to their placement.
Generalized danger areas were identified, with only the quantity of mines given in detail. Mines used in Operation Starvation were supposed to be self-sterilizing, but the circuit did not always work. Clearing the mines from Japanese waters took so many years that the task was eventually given to the Japan Maritime Self-Defense Force.
For the purpose of clearing all types of naval mines, the Royal Navy employed German crews and minesweepers from June 1945 to January 1948, organised in the
German Mine Sweeping Administration, the GMSA, which consisted of 27,000 members of the former Kriegsmarine and 300 vessels. Mine clearing wasn't always successful: a number of ships were damaged or sunk by mines after the war. Two such examples were the Liberty ships Pierre Gibault which was scrapped after hitting a mine in a previously cleared area off the Greek island of Kythira in June 1945, and Nathaniel Bacon which hit a minefield off Civitavecchia, Italy in December 1945, caught fire, was beached, and broke in two.
MINE
DAMAGE
The damage that may be caused by a mine depends on the "shock factor value", a combination of the initial strength of the explosion and of the distance between the target and the detonation. When taken in reference to ship hull plating, the term "Hull Shock Factor" (HSF) is used, while keel damage is termed "Keel Shock Factor" (KSF). If the explosion is directly underneath the keel, then HSF is equal to KSF, but explosions that are not directly underneath the ship will have a lower value of
KSF.
DIRECT DAMAGE
Usually only created by contact mines, direct damage is a hole blown in the ship. Among the crew, fragmentation wounds are the most common form of damage. Flooding typically occurs in one or two main watertight compartments which can sink smaller ships or disable larger ones. Contact mine damage often occurs at or close to the waterline near the bow, but depending on circumstances a ship could be hit anywhere on its outer hull surface (the USS Samuel B Roberts mine attack being a good example of a contact mine detonating amidships and underneath the ship).
BUBBLE JET EFFECT
The bubble jet effect occurs when a mine detonates in the water a short distance away from the ship. The explosion creates a bubble in the water, and due to the difference in pressure, the bubble will collapse from the bottom. The bubble is buoyant and so it rises towards the surface. If the bubble reaches the surface as it collapses it can create a pillar of water that can go over a hundred meters into the air (a "columnar plume"). If conditions are right and the bubble collapses onto the ship's hull the damage to the ship can be extremely serious; the collapsing bubble forms a high energy jet that can break a meter wide hole straight through the ship, flooding one or more compartments, and is capable of breaking smaller ships apart. The crew in the areas hit by the pillar are usually killed instantly. Other damage is usually limited.
The Baengnyeong incident, in which the ROKS Cheonan broke in half and sank off the coast South Korea in 2010, is thought by
some to have been caused by the bubble jet effect.
SHOCK EFFECT
If the mine detonates at a distance from the ship, the change in water pressure causes the ship to resonate. This is frequently the most deadly type of explosion, if it is strong enough.[citation needed] The whole ship is dangerously shaken and everything onboard is tossed around. Engines rip from their beds, cables from their holders, etc. A badly shaken ship usually sinks quickly, with hundreds, or even thousands of small leaks all over the ship and no way to power the pumps. The crew fare no better, as the violent shaking tosses them around. This shaking is powerful enough to cause disabling injury to knees and other joints in the body, particularly if the affected person stands on surfaces connected directly to the hull (such as steel decks).
The resulting gas cavitation and shock-front-differential over the width of the
human body is sufficient to stun or kill divers.
COUNTERMEASURES
Weapons are frequently a few steps ahead of countermeasures, and mines are no exception. In this field the British, with their large seagoing navy, have had the bulk of world experience, and most anti-mine developments, such as de-gaussing and the double-L sweep were British inventions. When on operational missions, such as the recent invasion of Iraq, the US still rely on British and Canadian
minesweeping services. The US has worked on some innovative mine hunting countermeasures, such as the use of military dolphins to detect and flag mines. However, they are of questionable effectiveness.
PASSIVE COUNTERMEASURES
Ships can be designed to be difficult for mines to detect, to avoid detonating them. This is especially true for minesweepers and mine hunters that work in minefields, where a minimal signature outweighs the need for armour and speed. These ships have hulls of glass fibre or wood instead of steel to avoid magnetic signatures, they use special propulsion systems, such as Voith-Schneider propellers, to limit the acoustic signature. They are built with hulls that produce a minimal pressure signature. These measures create other problems. They are expensive, slow, and vulnerable to enemy fire. Therefore, they need protection. Many modern ships have a mine-warning sonar—a simple sonar looking forward and warning the crew if it detects possible mines ahead. It is only effective when the ship is moving slowly.
A steel-hulled ship can be degaussed (more correctly, de-oerstedted or depermed) using a special degaussing station that contains many large coils and induces a magnetic field in the hull with alternating current to demagnetize the hull. This is a rather problematic solution, as magnetic compasses need recalibration and all metal objects must be kept in exactly the same place. Ships slowly regain their magnetic field as they travel through the Earth's magnetic field, so the process has to be repeated every six months.
A simpler variation of this technique, called wiping, was developed by Charles F. Goodeve which saved time and resources.
Between 1941 and 1943 the US Naval Gun factory (a division of the Naval Ordnance Laboratory) in Washington D.C. built physical models of all US Naval ships. Three kinds of steel were used in shipbuilding: mild steel for bulkheads, a mixture of mild steel and high tensile steel for the hull, and special treatment steel for armor plate. The models were placed within coils which could simulate the Earth's magnetic field at any location. The magnetic signatures were measured with degaussing coils. The objective was to reduce the vertical component of the combination of the Earth's field and the ship's field at the usual depth of German mines. From the measurements, coils were placed and coil currents determined to minimize the chance of detonation for any ship at any heading at any latitude.
Some ships are built with magnetic inductors, large coils placed along the ship to counter the ship's magnetic field. Using magnetic probes in strategic parts of the ship, the strength of the current in the coils can be adjusted to minimize the total magnetic field. This is a heavy and clumsy solution, suited only to small-to-medium sized ships. Boats typically lack the generators and space for the solution, while the amount of power needed to overcome the magnetic field of a large ship is impractical.
ACTIVE COUNTERMEASURES
Active countermeasures are ways to clear a path through a minefield or remove it completely. This is one of the most important tasks of any mine warfare flotilla.
MINE SWEEPING
A sweep is either a contact sweep, a wire dragged through the water by one or two ships to cut the mooring wire of floating mines, or a distance sweep that mimics a ship to detonate the mines. The sweeps are dragged by minesweepers, either purpose-built military ships or converted trawlers. Each run covers between one and two hundred meters, and the ships must move slowly in a straight line, making them vulnerable to enemy fire. This was exploited by the Turkish army in the Battle of Gallipoli in 1915, when mobile howitzer batteries prevented the British and French from clearing a way through minefields.
If a contact sweep hits a mine, the wire of the sweep rubs against the mooring wire until it is cut. Sometimes "cutters", explosive devices to cut the mine's wire, are used to lessen the strain on the sweeping wire. Mines cut free are recorded and collected for research or shot with a deck gun.
Minesweepers protect themselves with an oropesa or paravane instead of a second minesweeper. These are torpedo-shaped towed bodies, similar in shape to a Harvey Torpedo, that are streamed from the sweeping vessel thus keeping the sweep at a determined depth and position. Some large warships were routinely equipped with paravane sweeps near the bows in case they inadvertently sailed into minefields—the mine would be deflected towards the paravane by the wire instead of towards the ship by its wake. More recently, heavy-lift helicopters have dragged minesweeping sleds, as in the 1991 Persian Gulf War.
The distance sweep mimics the sound and magnetism of a ship and is pulled behind the sweeper. It has floating coils and large underwater drums. It is the only sweep effective against bottom mines.
During the Second World War, RAF Coastal Command used Vickers Wellington bombers Wellington DW.Mk I fitted with degaussing coils to trigger magnetic mines.
Modern influence mines are designed to discriminate against false inputs and are therefore much harder to sweep. They often contain inherent anti-sweeping mechanisms. For example, they may be programmed to respond to the unique noise of a particular ship-type, its associated magnetic signature and the typical pressure displacement of such a vessel. As a result, a mine-sweeper must accurately guess and mimic the required target signature in order to trigger detonation. The task is complicated by the fact that an influence mine may have one or more of a hundred different potential target signatures programmed into it.
Another anti-sweeping mechanism is a ship-counter in the mine fuze. When enabled, this allows detonation only after the mine fuze has been triggered a pre-set number of times. To further complicate matters, influence mines may be programmed to arm themselves (or disarm automatically—known as self-sterilization) after a pre-set time. During the pre-set arming delay (which could last days or even weeks) the mine would remain dormant and ignore any target stimulus, whether genuine or faked.
When influence mines are laid in an ocean minefield, they may have various combinations of fuze settings configured. For example, some mines (with the acoustic sensor enabled) may become active within three hours of being laid, others (with the acoustic and magnetic sensors enabled) may become active after two weeks but have the ship-counter mechanism set to ignore the first two trigger events, and still others in the same minefield (with the magnetic and pressure sensors enabled) may not become armed until three weeks have passed. Groups of mines within this mine-field may have different target signatures which may or may not overlap. The fuzes on influence mines allow many different permutations, which complicates the clearance process.
Mines with ship-counters, arming delays and highly specific target signatures in mine fuzes can falsely convince a belligerent that a particular area is clear of mines or has been swept effectively because a succession of vessels have already passed through safely.
MINE HUNTING
Mine hunting is very different from sweeping, although some minehunters can do both tasks. Mines are hunted using sonar, then inspected and destroyed either by divers or ROVs (remote controlled unmanned mini submarines). It is slow, but also the most reliable way to remove mines. Mine hunting started during the Second World War, but it was only after the war that it became truly effective.
Sea mammals (mainly the Bottlenose Dolphin) have been trained to hunt and mark mines, most famously by the U.S. Navy Marine Mammal Program. Mine-clearance dolphins were deployed in the Persian Gulf during the Iraq War in 2003. The Navy claims that these dolphins were effective in helping to clear more than 100 antiship mines and underwater booby traps from Umm Qasr Port.
French naval officer Jacques Yves Cousteau's Undersea Research Group was once involved in mine-hunting operations: They removed or detonated a variety of German mines, but one particularly defusion-resistant batch-equipped with acutely sensitive pressure, magnetic, and acoustic sensors and wired together so that one explosion would trigger the rest
- was simply left undisturbed for years until corrosion would (hopefully) disable the mines.
MINE BREAKING
A more drastic method is simply to load a cargo ship with cargo that makes her less vulnerable to sinking (wood for example) and drive her through the minefield, letting the ship to be protected follow the same path. This method was employed by the German Kriegsmarine during WWII, using converted ships known as Sperrbrecher ("barrage breaker"). Alternatively, a shallow draught vessel can be steamed through the minefield at high speed to generate a pressure wave sufficient to trigger mines, with the minesweeper moving fast enough to be sufficiently clear of the pressure wave so that triggered mines do not destroy the ship itself. These techniques are the only way to sweep pressure mines. The technique can be simply countered by use of a ship-counter, set to allow a certain number of passes before the mine is actually triggered. Modern doctrine calls for ground mines to be hunted rather than swept. A new system is being introduced for sweeping pressure mines however counters are going to remain a problem.
An updated form of mine breaking is the use of small unmanned ROVs that simulate the acoustic and magnetic signatures of larger ships and are built to survive exploding mines. Repeated sweeps would be required in case one or more of the mines had its "ship counter" facility enabled i.e. were programmed to ignore the first 2, 3, or even 6 target activations.
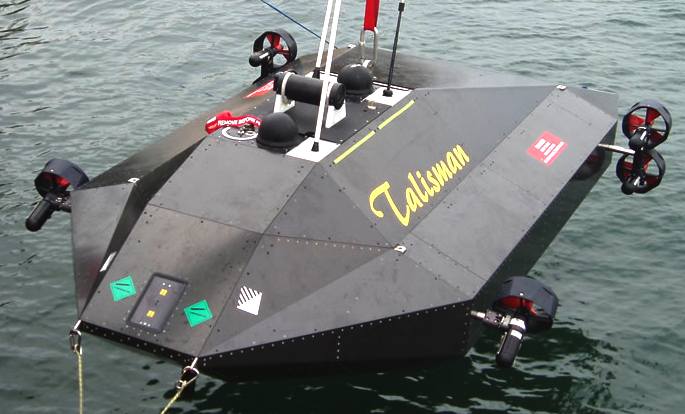
BAE Systems - Talisman mine hunter prototype
MINE
BUSTERS - 8 May 2007 -BAE SYSTEMS TALISMAN DEVELOPMENT PROGRAMME
BAE’s Talisman unmanned underwater vehicle aims to automate the work of clearing waters of dangerous mines to protect divers from harm.
During the first Gulf War, Iraq laced the Kuwait shoreline with tens of thousands of underwater mines in an attempt to stop US marines from landing. After the war, minesweepers removed more than 13,000 mines from the Persian Gulf but military officials believe there are many more to be found, presenting an ongoing danger to troops now stationed in the area.
However, dealing with the arsenal of underwater mines around the world is a terrifyingly dangerous business.
Despite the range of robotic options available to the world’s navies, in many cases mine clearance relies on specially-trained
scuba
divers, who swim down to visually identify the target or place explosive charges to dispose of it. Unsurprisingly, these missions are fraught with danger.
The latest tool to keep service personnel at a safe distance is the Talisman, an autonomous unmanned underwater vehicle (UUV) developed by BAE Systems, which can detect and destroy underwater mines. Its first production-ready model is being tested and it is hoped this car-sized robotic vehicle can help eliminate the need to use scuba divers in locating and destroying mines.
BAE System’s Andy Tonge is the Talisman’s project manager at the firm’s Underwater Systems Group, based at Waterlooville near Portsmouth. In his opinion mine warfare is a factor of more than just current conflicts; there are also many mines that have lain undiscovered since World Wars I and II.
‘Mine warfare is a war activity where the technology is very cheap and easy to use, so it will always be an issue,’ he said. ‘What we need is a technology that enables us to remotely operate from over the horizon with a degree of autonomy.’
Talisman is the combination of three phases of mine clearance technologies. One sonar-equipped vehicle is used to go out and locate mine-like objects, followed by a second vehicle equipped with cameras that can classify them. The third phase, which in some cases consists of little more than a trained clearance diver, is then engaged to dispose of the mine. Talisman is designed to combine these phases into one, sleek, manoeuvrable vehicle.
While Talisman is designed to autonomously detect and classify mine-like objects, human input is still required for the actual disposal, albeit from a distance. Upon the discovery of a mine, Talisman rises to the surface and transmits data via UHF radio to the command ship, which could be up to a few kilometres away. A human operator then controls the disposal technology — the BAE-designed remotely-operated vehicle called Archerfish.
Each Talisman vehicle is fitted with four ‘Archerfish’ single-shot mine neutralisers, which are connected to the Talisman via fibre optic cable. The
Archerfish goes in to video the suspected mine and this footage is transmitted back to the command ship. The operator on board the ship can then use the Archerfish to detonate a charge to dispose of the mine.
For Tonge it is crucial that a human operator takes control of this vital, final stage. ‘Even though the technology is very close to support full autonomous disposal of mines, you have to have a man in the loop to make sure first that it is a mine you are destroying and also to make sure it is done satisfactorily,’ he
is quoted as saying.
Although Talisman is built as a stealth submarine, it must rise to the surface before it can transmit video because underwater acoustic communications do not have the bandwidth to support video
streaming.
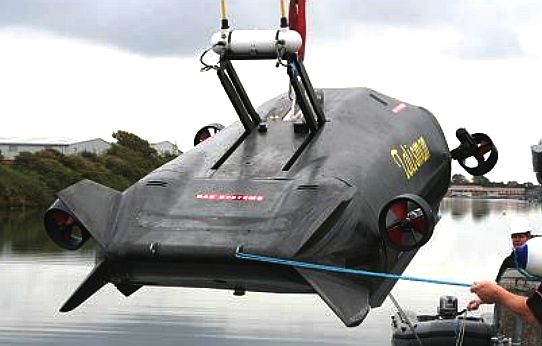
SPECIFICATIONS
The Talisman vehicle is based on an innovatively shaped
carbon fibre composite hull, with internal pressure vessels containing the electronics systems and payload. The stealthy hull design was based on BAE Systems’ aircraft technology. The vehicle weighs 1800kg, is approximately 4.5m long by 2.5m wide, can dive to 300m and has a top speed of 5 knots (9 km/h).
It is fitted with vectorable thruster pods, which allow it to manoeuvre very accurately in difficult conditions, including strong currents, and over an extended period of time: the Talisman can be deployed 50 miles offshore and remain in operation for 24
hours. The precise handling in all directions comes from six thrusters, two at the front, and four at the back in two pairs. A rotary actuator is used to vector each pair of thrusters and to operate the hydroplanes.
Talisman has been designed with a software architecture, which allows easy and rapid re-configuration of the mission
systems. All mission parameters are pre-settable before launch, for full autonomous operation, with the possibility of operator intervention throughout the mission.
Communications to and from the vehicle are via RF while the vehicle is surfaced and via acoustic communications systems when the vehicle is underwater.
The
vessel design has progress from the prototype in 2007, through 'L' to 'M'
model. You can see that the very basic hydrodynamics have improved to a
relatively streamlined fish.
Niall
Firth (The Engineer)
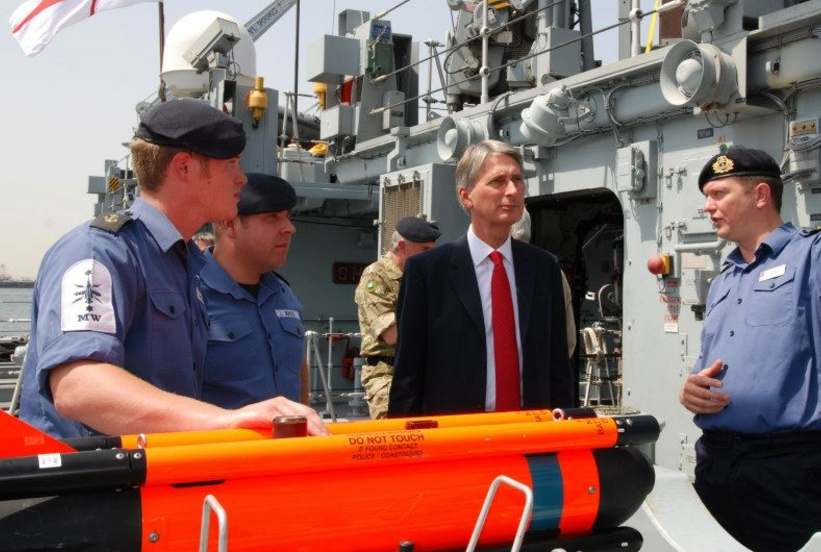
Philip Hammond visits HMS Ramsey and sees the Seafox mine disposal system
SEAFOX
The Seafox is a mine disposal unmanned underwater vehicle
(UUV) manufactured by Atlas Elektronik. The UUV was developed based on the expendable mine disposal vehicle
(EMDV) principle.
The semi-automatic UUV is primarily used for the disposal of mines and other identified ordnance in sea. It can detect and classify the mines and sea objects. It is guided by a
fibre-optic cable.
The SeaFox can also be used in damage estimation, intelligence, route survey, maritime boundary control and harbour surveillance missions.
The complete SeaFox system includes a console, a launcher, and the SeaFox vehicles. It can be launched from a range of naval platforms such as dedicated mine counter measures vessels
(MCM), surface combatants, rubber boats and helicopters.
The UK Ministry of Defence awarded a contract to Ultra Electronics and ATLAS in January 2006 to procure SeaFox UUV for the Royal Navy's Hunt class and Sandown class MCM vessels. The UUV is currently in service in more than ten countries.
The Royal Thai Navy (RTN) placed an order with Atlas Elektronik in December 2011 for three SeaFox mine disposal
UUVs.
The US Navy placed a contract with Lockheed Martin in February 2012 to adapt SeaFox UUV system for its MH-53E Dragon mine hunting helicopter and the Avenger-class MCM vessel.
The US Naval Surface Weapons Centre (NSWC) awarded a contract for additional SeaFox vehicles to support its Surface Mine Neutralisation System
(SMNS), in October 2012. The SeaFox UUVs were deployed by the US Navy in the Persian Gulf in 2012 to clear the mines.

SEAFOX VARIANTS
SeaFox is mainly offered in four variants to meet the different mission requirements of users. The variants include SeaFox C, Sea Fox I, SeaFox T and SeaFox COBRA.
The SeaFox C is a one-shot mine identification and disposal vehicle system used as a tool to semi-automatically dispose mines and other related things found in the sea. It can quickly relocate the identified objects using onboard homing sonar. Once relocated, these objects are destroyed using an inbuilt, large
calibre-shaped charge of the vehicle. The vehicle is powered by a non-rechargeable LiSO2 battery.
Sea Fox I is a mine identification, inspection and training UUV. It is a reusable vehicle, which can be used to identify the mines and train the field staff. It is fitted with a ballast weight instead of a warhead.
SeaFox T is a training version of the SeaFox C. It is intended to train onboard naval crew members to operate the SeaFox C.
SeaFox COBRA is equipped with the COBRA explosive ordnance disposal (EOD) tool supplied by ECS Special Projects. The vehicle has a remote
RF-coded initiation capability with a range of up to 1.5km for commercial use and up to 22km for military use. The target is attached to the vehicle in three ways, which include nail attachment units, harpoon for soft-skinned targets and magnetic grabs.
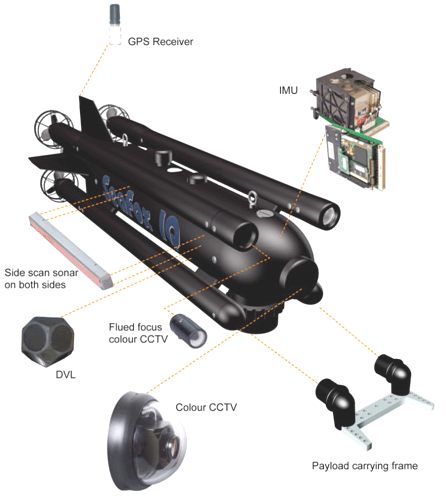
SEAFOX FEATURES
All the variants of the SeaFox UUV have a similar physical design and dimensions. The UUV has an overall length of 1.31m and width of 0.39m. It is designed with a height of 0.39m, and weighs approximately 43kg.
The UUV can be operated at a depth of up to 300m. It can operate at a maximum speed of 6kt. It has a maximum endurance of 100 minutes depending on the assignment and other conditions.
SEAFOX NAVIGATION & SENSORS
The SeaFox mine disposal systemuses transponder/responder aided dead reckoning (pressure sensor) for navigation in the sea. The operator communicates with the SeaFox using a
fibre-optic cable.
The SeaFox is equipped with FLS sensors and a TV camera to identify the target and acquire related information.
SEAFOX PROPULSION
The vehicle includes four independent reversible motors and a hover thruster which provides high manoeuvrability in reaching the desired position.
Both SeaFox C and SeaFox COBRA are powered by non-rechargeable LiSO2 battery, while Sea Fox I and SeaFox T variants use rechargeable NiMH batteries.
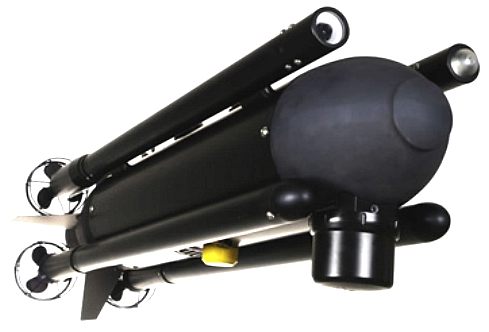
SEAFOX
STRATEGY - OCTOBER 2012
The recent massive naval mine clearing exercise in the mouth of the
Persian Gulf (the Straits of
Hormuz) demonstrated two things. First, mine clearing ships (which many nations have) and mine clearing helicopters (like the U.S. MH-53) were not as successful as hoped. A lot of the practice mines used were not found. Second, one new system, the SeaFox (a remotely controlled underwater system) was very successful. Ten nations already have
SeaFox, and while the United States is a new user, it is hustling to make SeaFox work from different ships and aircraft. This involves training ship crews to operate SeaFox and equipping ships with the control equipment.
Earlier this year the
U.S. Navy ordered several dozen more of the expendable SeaFox UUVs (unmanned underwater vehicles). SeaFox was designed to find and destroy bottom mines (which sit on the seabed) as well as those that float. These UUVs were quickly sent to the Persian Gulf to deal with potential Iranian use of naval mines. The U.S. first used their new Seafox UUVs on some of the eight U.S. Avenger class mine hunting ships stationed in the Persian Gulf.
SeaFox is a small (1.4x.4x.2 meters/55x16x8 inches) battery powered sub that weighs 43 kg (95 pounds) and has a fiber-optic cable connecting it to a surface ship or hovering
helicopter. The controller can move the SeaFox close to a suspected mine (using a small sonar unit to assist navigation), then turn on a spotlight for a video cam to examine the object and determine if it is a mine. If it is then SeaFox gets closer and detonates a shaped charge explosive, sending a shaft of hot plasma through the mine destroying it (and the
SeaFox).
SeaFox has an endurance of about 100 minutes, a top speed of 10
kilometers an hour, and can dive as deep as 300 meters (930 feet). Operators get to increase their skills and effectiveness using a SeaFox simulator.
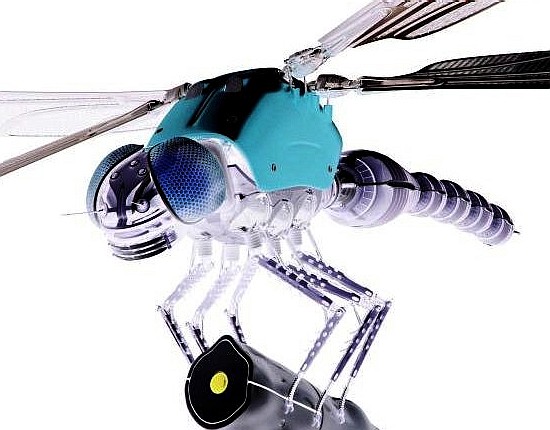
The
proposed Dragonfly ASV mine hunting system is based on the patent 'Bluefish' energy
harvesting platform and SNAV to provide low cost persistent monitoring of
key routes. Once NATO has proven that autonomous mine countermeasures is
the way to go, this is the next logical development in unmanned and cost
effective persistence monitoring.
LATEST
DEVELOPMENTS
LONG
RANGE AUTONOMOUS
MINE HUNTING & SWEEPING
The
latest innovation (2013) in mine neutralization is another British
invention that combines existing techniques within a surface platform that
uses energy from nature and advanced autonomous technology to search near continuously
for mines without the need for a crew and as a 'world' fleet exercise
coordinated by a central command. Such a vessel combined as a coordinated
fleet cuts the cost of the persistent monitoring that is necessary to
ensure that submarine and other fleet and commercial corridors are free of
mines that may have been planted by, among other enemies, radical groups
(terrorists).
The
development of this technology is ongoing to not only improve the quality
of mine disposal and effectiveness, but also to reduce the cost of
operations for organisations such as NATO
and the pollution caused by the military who now also recognize that they
owe a duty (MARPOL)
to the environment.
Without
continuous forward development opposing forces might easily take the
strategic lead with tactics in place developed using disruptive technology
that allied forces are through lack of proactive impetus may be caught off
guard.
MINE
STOCK & DEVELOPMENT
US
MINES
The United States Navy MK56 ASW mine (the oldest still in use by the US) was developed in 1966. More advanced mines include the MK60 CAPTOR (short for "encapsulated torpedo"), the MK62 and MK63 Quickstrike and the MK67 SLMM (Submarine Launched Mobile Mine). Today, most U.S. naval mines are delivered by aircraft.
UK
MINES
According to a statement made to the
UK Parliament in 2002:
"...the Royal Navy does not have any mine stocks and has not had since 1992. Notwithstanding this, the United Kingdom retains the capability to lay mines and continues research into mine exploitation. Practice mines, used for exercises, continue to be laid in order to retain the necessary skills".
However, a British company (BAE
Systems) does manufacture the Stonefish influence mine for export to friendly countries such as Australia, which has both war stock and training versions of Stonefish, in addition to stocks of smaller Italian MN103 Manta mines. The computerised fuze on a Stonefish mine contains acoustic, magnetic and water pressure displacement target detection sensors. Stonefish can be deployed by fixed-wing aircraft, helicopters, surface vessels and submarines. An optional kit is available to allow Stonefish to be air-dropped, comprising an aerodynamic tail-fin section and parachute pack to retard the weapon's descent. The operating depth of Stonefish ranges between 30 and 200
metres. The mine weighs 990 kilograms and contains a 600 kilogram aluminised PBX explosive warhead.

SUBMARINE
INDEX
Alvin
DSV - Woods Hole Oceanographic Institution
HMS
Astute 1st of Class
BAE Systems
HMS
Vanguard- Trident
INS
Sindhurakshak - explosion
& sinking
Lusitania
- Torpedo
attack
Nuclear
submarines lost
at sea
Predator
- Covert submarine hunter/killer
Seawolf
- Autonomous wolf pack deployment of Predator mini-subs
Torpedoes
- UUV anto submarine weapons
U20
- Kapitan Leutnant Walther Schwieger
USS
Bluefish WWI submarine
USS
Bluefish - Nuclear submarine
USS
Flying Fish
USS
Jimmy Carter - Seawolf class fast attack nuclear submarine
USS
Nautilus - 1st nuclear submarine & subsea north pole passage
LINKS
& REFERENCE
Marine
Link news underwater-unlocking
http://www.marinelink.com/news/underwater-unlocking378339.aspx
US
Navyrobot mine ship
http://www.wired.co.uk/news/archive/2013-01/04/navy-robot-ship
http://www.royalnavy.mod.uk/The-Fleet/Ships/Weapons-Systems/Sea-Fox
http://www.naval-technology.com/projects/seafox-mine-disposal/
Wikipedia
Talisman_UUV
The
Engineer mine busters
http://en.wikipedia.org/wiki/Talisman_UUV
http://www.theengineer.co.uk/in-depth/mine-busters/299583.article
http://www.history.navy.mil/wars/korea/minewar.htm
http://www.time.com/time/magazine/article/0,9171,926817,00.html
The_Corfu_Channel_Case_(UK_v._People_Republic_of_Albania)
Wikipedia
United_States_Navy
Wikipedia
HMHS_Britannic
Wikipedia
Admiralty_Mining_Establishment
Wikipedia
Naval_mine
Enterprise
Europe Scotland sct news
http://en.wikipedia.org/wiki/United_States_Navy
http://en.wikipedia.org/wiki/HMHS_Britannic
http://en.wikipedia.org/wiki/Admiralty_Mining_Establishment
http://en.wikipedia.org/wiki/Naval_mine
http://www.enterprise-europe-scotland.com/sct/news/?newsid=4306
Mine
countermeasures
- Youtube
|
|