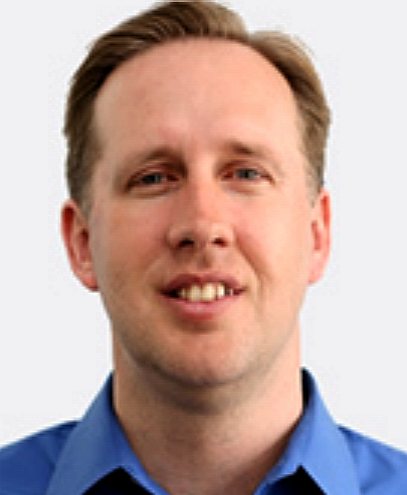
ASI
President and CEO Mel Torrie
HISTORY
For more than 12 years, Autonomous Solutions, Inc. has been a world leader in unmanned ground vehicle systems and components. From their northern Utah headquarters, ASI serves clients in military, agriculture, industrial, and automotive proving ground industries with solutions ranging from remote controlled to fully autonomous vehicles.
ASI was established in 2000, winning their first contract with John Deere.
They are a company specializing in land vehicle control. This first
contract was the start of a rapid growth and development period. Three
years later, in April of 2003 they released Mobius,™ a Command & Control
software to replace the legacy MARS system. In the same year, in June,
they were granted a patent
by the USPTO for their orchard automation technology, which is found in the John Deere 5510.
FInally in October 2003 ASI released its first version of Chaos,™ a high
mobility robot.
From
July 2005, ASI worked with the Nellis Air Force Base to develop the JT3 automated targeting vehicles.
Robots make ideal moving targets, the by product of which is that
companies get to develop the systems for more advanced applications,
leading to autonomy.
Two
years later in March of 2007 ASI moved to their new 100 acre headquarters and proving ground in
Petersboro, Utah. In this year ASI participated in the 2007 DARPA Grand Challenge
(Urban
Challenge). In February ASI were named the MEP Utah Manufacturer of the Year for 2006.
October
2008 saw ASI introduce vehicle automation options into the mining/industrial market.
Then there is a break until they found the vehicle Proving Ground
Automation entity in January of 2011. This is for their developments in
the automotive testing industry. In August of 2011 with Team UXOD (ASI,
SAIC, Kairos Autonomi, and Zonge International) they won the 2011 Robotic Range Clearance Competition.
Significantly,
in February of 2012 the USPTO granted ASI a patent for their Guideline™ Robotic Convoy System.
In December of ASI adopted their AGILE design processes for both hardware and software development,
under the trade name Guideline.™
In
April of 2013 the Guideline™ Robotic Convoy System was named the Bronze Edison Award winner
in the Applied Technology (Safety Category). There is thus a clear pattern
of development heading toward autonomy of vehicles. Where this may lead is
anyone's guess, ultimately dependent on market trends.
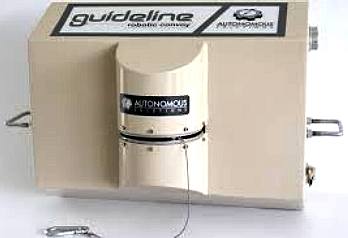
EDISON
AWARDS - CHICAGO, IL (PRWEB) March 25, 2013
Guideline™ Robotic Convoy System has been named a 2013 Award Finalist by the internationally renowned Edison Awards™. Guideline™ by Autonomous Solutions, Inc. (ASI) is a Finalist in the Applied Technologies (Safety) category, one of twelve categories honored by the Edison Awards™. The distinguished awards symbolize the persistence and excellence personified by
Thomas Alva
Edison, inspiring creative minds to remain in the forefront of innovation, creativity and ingenuity in the global economy.
“More than any year, this year’s slate of Finalists demonstrate the enormous value of teamwork, experimentation, consumer focus, market awareness and game-changing success,” said Frank Bonafilia, Edison Awards’ executive director. “It’s exciting to see companies like Autonomous Solutions continuing Thomas Edison’s legacy of challenging conventional thinking.”
“This is a great honor to be selected as an Edison Award Finalist,” said Mel Torrie, CEO of ASI. “Guideline is a simple, but innovative solution to autonomous convoying that will save lives and also increase productivity. We’re excited that the Edison Award Panelists also recognized Guideline’s benefits and potential.”
The ballot of nominees for the Edison Awards™ is judged by more than 3,000 senior business executives and academics from across the nation whose votes acknowledge the Finalists’ success in meeting the award criteria of Concept, Value, Delivery and Impact. The Panel includes members of the Marketing Executives Networking Group (MENG), the American Association Advertising Agencies (4As) the Chief Marketing Officer Council (CMO), the Design Management Institute (DMI), the American Productivity & Quality Center (APQC) the American Society of Mechanical Engineers (ASME) and the Association of Technology Management & Applied Engineering (ATMAE). Also on the Panel are hundreds of past Edison Award winners, marketing professionals, scientists, designers, engineers and academics.
Award winners will be announced April 25, 2013, at the Edison Awards Annual Gala, held in the Grand Ballroom at historic Navy Pier in Chicago, IL.
The Edison Awards™ is a program conducted by Edison Universe, a 501(c)(3) charitable organization dedicated to fostering future innovators. The 2013
Edison Awards are sponsored by Nielsen, Discovery Communications, Science Channel, and USA Today.
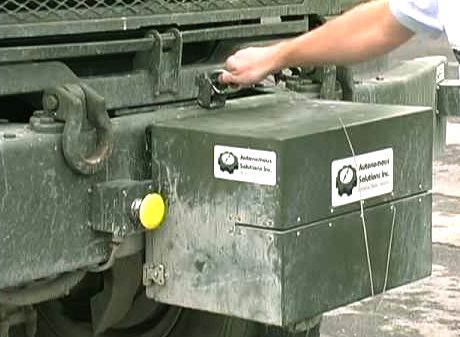
US PATENT CONVOY
The Guideline Unmanned Convoy System extends instant and highly-featured advantages to industrial as well as military operators such as high efficiency in non-combat or industrial zones; minimization in driving personnel by over 2X. It also provides failsafe, redundant leader-follower system, equipping GPS/laser guided convoy systems during interference or when signal is lost; and protecting military personnel from dangers within active combat zones. The system ensures effective operation in all types of road conditions, terrain, and weather. Furthermore, it is compatible with all sizes of vehicles from small ATVs to well-built, sturdy military transport vehicles.
This robotically-controlled guidance system called ‘Guideline system’ can be installed atop the anterior part of military or industrial vehicles. Each Guideline unit is composed of Kevlar tether equipped on a mechanical spool. The unit also includes sensors that can clearly examine the speed, vector, and length of the tether that moves from or returns to the spool, based on the data to the automation kit of the vehicle. The onboard computer built within the kit shows the speed and position of the lead vehicle, designing a course for the autonomous vehicle that imitates the actual path of the leader. Once the lead vehicle is propelled for motion, the buffer distance between the two vehicles is automatically increased by the Guideline, ensuring safe stopping distance.
ASI’s Guideline Robotic Convoy System is now being deployed in field trials in Singapore, the United States, and Australia, serving various operation scenarios.

TRADEMARK
- GUIDELINE ROBOTIC CONVOY
Word
Mark:
|
GUIDELINE
ROBOTIC CONVOY
|
Status/
Status Date:
|
PUBLICATION/ISSUE
REVIEW COMPLETE
|
Serial
Number:
|
85864421
|
Filing
Date:
|
3/1/2013
|
Registration
Number:
|
NOT
AVAILABLE
|
Registration
Date:
|
NOT
AVAILABLE
|
Goods
and Services:
|
autonomous
leader/follower robotic software and hardware system comprised
of communication software for creating algorithms to determine
distance, vector, speed, and position of lead vehicle, plotting
course for following vehicle, and relay of commands to
autonomous computer and tether spool, tether attachment device,
sensors, sold as a unit
|
Mark
Description:
|
The
mark consists of The large word "GUIDELINE" is lower
case. A graphical depiction of a carabineer is attached to the
lower part of the "G" of "GUIDELINE". A
straight dotted line leads from the carabineer to an oval,
dotted line shape that surrounds the words "ROBOTIC
CONVOY".
|
Type
Of Mark:
|
TradeMark
|
Published
For Opposition Date:
|
2/4/2014
|
Last
Applicant/Owner:
|
Autonomous
Solutions, Inc.
Petersboro, UT 84325
|
Mark
Drawing Code:
|
Drawing/Design
+ Words
|
Design
Search: |
Other
small hardware articles, including hooks, magnets (Hardware,
tools and ladders, non - motorized agricultural implements;
keys and locks. - Small hardware articles, springs )
Oblongs
as carriers for words, letters or designs. (Geometric figures
and solids - Rectangles)
Dotted
line(s) (Geometric figures and solids - Lines, bands, bars,
chevrons and angles)
Horizontal
line(s), band(s) or bar(s) (Geometric figures and solids -
Lines, bands, bars, chevrons and angles)
|
Register
Type:
|
Principal
|
Disclaimer:
|
("ROBOTIC
CONVOY")
|
Correspondent:
|
AUTONOMOUS
SOLUTIONS, INC.
AUTONOMOUS
SOLUTIONS, INC.
|
CLASSIFICATION
INFORMATION
International
Class Code(s):
|
009
|
US
Class Code(s):
|
021,
023, 026, 036, 038
|
Primary
Class:
|
Scientific,
nautical, surveying, photographic, cinematographic,
optical, weighing, measuring, signalling, checking
(supervision), life-saving and teaching apparatus and
instruments; apparatus and instruments for conducting,
switching, transforming, accumulating, regulating or
controlling electricity; apparatus for recording,
transmission or reproduction of sound or images;
magnetic data carriers, recording discs; automatic
vending machines and mechanisms for coin operated
apparatus; cash registers, calculating machines, data
processing equipment and computers; fire extinguishing
apparatus.
|
Class(es)
Status:
|
Active
|
First
Use Anywhere:
|
5/1/2008
|
First
Use In Commerce:
|
7/14/2008
|
|
COLLABORATION
As
a company ASI is open to partnering and collaborative research. Of
particular interest to those into vehicle control are the following areas
of development:
3D ROBOTIC PERCEPTION
Obstacle Detection
Left to themselves, blind unmanned vehicles might run over or into obstacles in the course of their
pathway. ASI's Forecast 3D Laser System and Vantage obstacle detection and avoidance
software enables unmanned vehicles to detect objects that could pose a threat and react appropriately. Depending on vehicle
configuration, unmanned vehicles may exhibit see-and-stop or see-and-avoid behavior when encountering an obstacle.
GPS-Denied Autonomy
ASI researchers claim to be at the forefront of the industry in designing new methods for GPS-denied navigation. Advanced navigation systems
include position estimation from multi-sensor fusion and road detection algorithms that allow navigation regardless of GPS
quality. Other research areas include autonomous object avoidance with no operator
communication and indoor positioning. These methods will be valuable for explosive disposal, combat surveillance, hazmat
cleanup, and search and rescue applications.
UNMANNED MILITARY SOLUTIONS
Tactical Response - Fast acting and precision response can save lives in
military situations. ASI's automated tactical units shield personnel from danger while providing critical advantages
against opposing dangers.
Robotic Convoy - Removing soldiers from combat zones to improve efficiency for
logistical operations, for example with robotic convoys. ASI's Guideline™
Robotic Convoy System and vehicle automation kits are force multipliers and safety enhancers.
Training/Targeting - Enable moving target, live-fire training for military operations in
all branches. Autonomous vehicles can tow targeting skids or can be targets themselves for training missions that target moving vehicle
convoys.
Security
- Improve perimeter or border security by implementing autonomous vehicle technology.
Automated ATVs or patrol vehicles can scan for intruders, execute EOD missions, and perform vehicle and personnel
inspections at checkpoints.
Robots save lives. Unmanned vehicles provide critical, real-time data, giving soldiers superior tactical advantage in dangerous circumstances. In some cases, robots remove humans completely from danger by allowing them to handle combat situations and perform other tasks from a safe distance.
VEHICLE AUTOMATION
The
ASI vehicle automation kit is a set of universal, rugged automation components that enable robotic steering, transmission, speed, and brake.
Mobius™ Command & Control Software:
* Controls multiple vehicles in the proving ground
* Collects testing data
* Monitors vehicle health
* Sets driver performance benchmarks
Performs automated testing events, including: durability, destructive rollover, high speed, mileage accumulation, and ADAS.
Full Autonomy
- Autonomous vehicles improve proving ground safety. Some durability tests are so strenuous that they have hospitalized drivers. Our automation technology allows researchers to protect drivers
while still performing rigorous testing events. Researchers also set precise pathways and repeat events multiple times in a row while maintaining high levels of accuracy.
Manual Toggle
- When transferring vehicles from one event to another and interacting with manned traffic onsite, drivers improve safety by toggling to manual mode, and then back to auto when positioned for testing.
Site Management
- Using robotic technology, proving ground site managers can set benchmarks to test performance, collect data for reporting and analytics, and monitor vehicle health information.
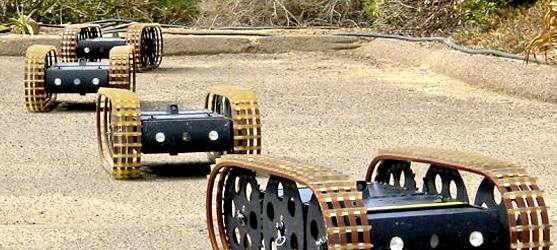
ROBOT
GUIDANCE PATENT 8,116,921
United
States Patent
|
8,116,921
|
Ferrin
, et al.
|
February
14, 2012
|
Follower
vehicle control system and method for forward and reverse convoy
movement
Abstract
A
vehicle control system for causing a follower vehicle to follow a
leader may have a tether system mounted to the follower vehicle.
The tether system may include a tether having an end adapted to be
attached to the leader, a length sensor, and an angle sensor. A
path tracking system operatively associated with the tether system
determines a path traveled by the leader. A path control system
operatively associated with the path tracking system and the
follower vehicle causes the follower vehicle to follow the path
traveled by the leader. A spacing control system operatively
associated with the path tracking system and the follower vehicle
causes the follower vehicle to maintain a predetermined spacing
between the follower vehicle and the leader.
Inventors:
|
Ferrin;
Jeffrey L. (Petersboro, UT), Thayn; Brett (Petersboro,
UT), Hornberger; Michael (Petersboro, UT)
|
Assignee:
|
Autonomous
Solutions, Inc. (Petersboro, UT)
|
Family
ID:
|
41697118
|
Appl.
No.:
|
12/238,733
|
Filed:
|
September
26, 2008
|
Prior
Publication Data
|
|
|
|
Document
Identifier
|
Publication
Date
|
|
US
20100049374 A1
|
Feb
25, 2010
|
|
Related
U.S. Patent Documents
|
|
|
|
|
|
|
|
|
|
|
Application
Number
|
Filing
Date
|
Patent
Number
|
Issue
Date
|
|
61189527
|
Aug
20, 2008
|
|
|
|
61091273
|
Aug
22, 2008
|
|
|
|
Current
U.S. Class:
|
701/1
; 242/390.8; 242/412; 701/494; 701/96
|
Current
CPC Class:
|
G05D
1/0227 (20130101); G05D 1/0293 (20130101); G05D
1/0272 (20130101); G05D 1/0278 (20130101); G05D
2201/0213 (20130101)
|
Current
International Class:
|
G05D
1/00 (20060101)
|
References
Cited [Referenced
By]
U.S.
Patent Documents
Other References
Dudek, G., et al., "Experiments in Sensing and
Communication for Robot Convoy Navigation," IEEE,
1995, pp. 268-273. cited by other .
Sorensen, David Kristin, et al., "On-Line Optical
Flow Feedback for Mobile Robot
Localization/Navigation," IEEE, 2003, pp. 1246-1251.
cited by other .
Wu, Jianping, et al., "Vehicle to Vehicle
Communication Based Convoy Driving and Potential
Applications of GPS," IEEE, Autonomous Decentralized
System, IEEE, 2002, pp. 212-217. cited by other .
Hedrick, J.K., et al., "Vehicle Modeling and Control
for Automated Highway Systems," Tech. Rep.,
University of California, Berkley, 1993. cited by other .
Tan, Han-Shue, et al., "Vehicle Lateral Warning, Guidance
and Control Based on Magnetic Markers: PATH Report of
AHSRA Smart Cruise 21 Proving Tests," Tech Rep.,
University of California, Berkley, 2001. cited by other .
Cowan, Noah, et al., "Vision-based
Follow-the-Leader," IEEE, 2003, pp. 1796-1801. cited
by other .
Belkhouche, Feihi, et al., "Modeling and Controlling
a Robotic Convoy Using Guidance Laws
Strategies," IEEE Transactions on Systems, Man and
Cybernetics, vol. 35, 2005, pp. 813-825. cited by other .
Debenest, Paulo, et al., "Proposal for Automation of
Humanitarian Demining with Buggy Robots,"
IEEE, 2003, pp. 329-334. cited by other .
Fukushima, Edwardo, F., et al., "A New Flexible
Component for Field Robotic System," IEEE
Proceedings, 2003, pp. 2583-2588. cited by other .
Hedrick, J.K., et al., "Control Issues in Automated
Highway Systems," IEEE, 1994, pp. 21-32. cited by
other .
Mariottini, Gian Luca, et al., "Vision-based
Localization of Leader-Follower Formations," IEEE,
2005, pp. 635-640. cited by other .
Doh, Nakju, et al., "Accurate Relative Localization
Using Odometry," IEEE Proceedings, 2003, pp.
1606-1612. cited by other .
Borenstein, J., et al., "Gyrodometry: A New Method
for Combining Data from Gyros and Odometry in Mobile Robots,"
IEEE, 1996, pp. 423-428. cited by other .
Coulter, R. Craig, "Implementation of the Pure
Pursuit Path Tracking Algorithm," Tech. Rep.,
Carnegie Mellon University, 1992, 11 pages. cited by
other.
|
Primary Examiner: Zanelli; Michael J.
Attorney, Agent or Firm:
Fennemore Craig, P.C.
Parent
Case Text
REFERENCE TO CO-PENDING PROVISIONAL APPLICATIONS
Applicants hereby claim the benefit of earlier filed co-pending
provisional applications, Application No. 61/189,527, filed on
Aug. 20, 2008, and Application No. 61/091,273, filed Aug. 22,
2008, both of which are specifically incorporated herein by
reference for all that they disclose.
Claims
The invention claimed is:
1. A vehicle control system for causing a follower vehicle to
follow a leader, comprising: a tether system mounted to the
follower vehicle, said tether system comprising: a tether having
an end adapted to be attached to the leader; a length sensor
operatively associated with said tether, said length sensor
sensing a length of said tether extending between the follower
vehicle and the leader; and an angle sensor operatively associated
with said tether, said angle sensor sensing an angle between said
tether and the follower vehicle; a path tracking system
operatively associated with said tether system, said path tracking
system determining a path traveled by the leader; a path control
system operatively associated with said path tracking system and
the follower vehicle, said path control system causing the
follower vehicle to follow the path traveled by the leader; a
spacing control system operatively associated with said path
tracking system and the follower vehicle, said spacing control
system causing the follower vehicle to maintain a predetermined
spacing between the follower vehicle and the leader; and a dead
reckoning system operatively associated with the follower vehicle,
said path tracking system, and said path control system, said dead
reckoning system producing position and heading estimates of the
follower vehicle.
2. The system of claim 1, wherein said dead reckoning system
comprises an odometer and a steering angle sensor.
3. The system of claim 1, wherein said dead reckoning system
comprises an odometer and a heading gyroscope.
4. A vehicle control system for causing a follower vehicle to
follow a leader, comprising: a tether system mounted to the
follower vehicle, said tether system comprising: a tether having
an end adapted to be attached to the leader; a length sensor
operatively associated with said tether, said length sensor
sensing a length of said tether extending between the follower
vehicle and the leader; and an angle sensor operatively associated
with said tether, said angle sensor sensing an angle between said
tether and the follower vehicle; a path tracking system
operatively associated with said tether system, said path tracking
system determining a path traveled by the leader; a path control
system operatively associated with said path tracking system and
the follower vehicle, said path control system causing the
follower vehicle to follow the path traveled by the leader; a
spacing control system operatively associated with said path
tracking system and the follower vehicle, said spacing control
system causing the follower vehicle to maintain a predetermined
spacing between the follower vehicle and the leader; and a
direction control system operatively associated with the follower
vehicle and said tether system, said direction control system
selecting between a forward travel direction and a reverse travel
direction for the follower vehicle based on a change in length of
said tether.
5. A vehicle control system for causing a follower vehicle to
follow a leader, comprising: a tether system mounted to the
follower vehicle, said tether system comprising: a tether having
an end adapted to be attached to the leader; a length sensor
operatively associated with said tether, said length sensor
sensing a length of said tether extending between the follower
vehicle and the leader; and an angle sensor operatively associated
with said tether, said angle sensor sensing an angle between said
tether and the follower vehicle, a path tracking system
operatively associated with said tether system, said path tracking
system determining a path traveled by the leader; a path control
system operatively associated with said path tracking system and
the follower vehicle, said path control system causing the
follower vehicle to follow the path traveled by the leader; a
spacing control system operatively associated with said path
tracking system and the follower vehicle, said spacing control
system causing the follower vehicle to maintain a predetermined
spacing between the follower vehicle and the leader; and a damper
operatively associated with said angle sensor.
6. A vehicle control system for causing a follower vehicle to
follow a leader, comprising: a tether mounted to the follower
vehicle, said tether having an end adapted to be attached to the
leader; length sensing means operatively associated with said
tether for sensing a length of said tether extending between the
follower vehicle and the leader; angle sensing means operatively
associated with said tether for sensing an angle between said
tether and the follower vehicle; a path tracking system
operatively associated with said length sensing means and said
angle sensing means, said path tracking system determining a path
traveled by the leader; a path control system operatively
associated with said path tracking system and the follower
vehicle, said path control system causing the follower vehicle to
follow the path traveled by the leader; a spacing control system
operatively associated with said path tracking system and the
follower vehicle, said spacing control system causing the follower
vehicle to maintain a predetermined spacing between the follower
vehicle and the leader; and a dead reckoning system operatively
associated with the follower vehicle, said path tracking system,
and said path control system, said dead reckoning system producing
position and heading estimates of the follower vehicle.
7. A method for causing a follower vehicle to follow a leader,
comprising: connecting the follower vehicle to the leader with a
tether; measuring a length of the tether connecting the follower
vehicle to the leader; measuring an angle between the tether and
the follower vehicle; determining a position of the leader based
on the measured length and the measured angle; determining a path
traveled by the leader based on a plurality of determined leader
positions; steering the follower vehicle so that the follower
vehicle substantially follows the path traveled by the leader,
wherein steering the follower vehicle comprises: determining an
actual position of the follower vehicle; comparing the actual
position of the follower vehicle with a desired position of the
follower vehicle to determine an off-path error; using the
off-path error to calculate a desired curvature; and using the
desired curvature to produce a steering command for the follower
vehicle; and controlling a velocity of the follower vehicle so
that the follower vehicle maintains a predetermined distance from
the leader.
8. The method of claim 7, wherein using the off-path error to
calculate a desired curvature comprises: establishing a look-ahead
length; using the look-ahead length to identify a look-ahead point
on the path traveled by the leader; and using the look-ahead point
to determine the off-path error.
9. The method of claim 8, wherein the look-ahead length is a
function of the velocity of the follower vehicle.
10. A method for causing a follower vehicle to follow a leader,
comprising: connecting the follower vehicle to the leader with a
tether measuring a length of the tether connecting the follower
vehicle to the leader; measuring an angle between the tether and
the follower vehicle; determining a position of the leader based
on the measured length and the measured angle; determining a path
traveled by the leader based on a plurality of determined leader
positions; steering the follower vehicle so that the follower
vehicle substantially follows the path traveled by the leader; and
controlling a velocity of the follower vehicle so that the
follower vehicle maintains a predetermined distance from the
leader, wherein controlling the velocity of the follower vehicle
comprises: determining an actual length between the leader and the
follower vehicle, the actual length being measured along the path
traveled by the leader; determining a desired length between the
leader and the follower vehicle, the desired length being measured
along the path traveled by the leader; comparing the actual length
and the desired length to determine a vehicle spacing error; and
using the vehicle spacing error to control the velocity of the
follower vehicle.
11. A method for causing a follower vehicle to follow a leader,
comprising: connecting the follower vehicle to the leader with a
tether; measuring a length of the tether connecting the follower
vehicle to the leader; measuring an angle between the tether and
the follower vehicle; determining a position of the leader based
on the measured length and the measured angle; determining a path
traveled by the leader based on a plurality of determined leader
positions; steering the follower vehicle so that the follower
vehicle substantially follows the path traveled by the leader;
controlling a velocity of the follower vehicle so that the
follower vehicle maintains a predetermined distance from the
leader; operating the follower vehicle in a reverse travel
direction; and steering the follower vehicle in the reverse travel
direction to follow in reverse at least a portion of the path
traveled by the leader.
12. A method for causing a follower vehicle to follow a leader,
comprising: connecting the follower vehicle to the leader with a
tether; measuring a length of the tether connecting the follower
vehicle to the leader; measuring an angle between the tether and
the follower vehicle; determining a position of the leader based
on the measured length and the measured angle; determining a path
traveled by the leader based on a plurality of determined leader
positions; steering the follower vehicle so that the follower
vehicle substantially follows the path traveled by the leader;
controlling a velocity of the follower vehicle so that the
follower vehicle maintains a predetermined distance from the
leader; operating the follower vehicle in a reverse travel
direction; and steering the follower vehicle in the reverse travel
direction based on the measured angle between the tether and the
follower vehicle.
13. A method for causing a follower vehicle to follow a leader,
comprising: connecting the follower vehicle to the leader with a
tether; measuring a length of the tether connecting the follower
vehicle to the leader; measuring an angle between the tether and
the follower vehicle; determining a position of the leader based
on the measured length and the measured angle; determining a path
traveled by the leader based on a plurality of determined leader
positions; steering the follower vehicle so that the follower
vehicle substantially follows the path traveled by the leader;
controlling a velocity of the follower vehicle so that the
follower vehicle maintains a predetermined distance from the
leader; and selecting to operate the follower vehicle in either a
forward travel direction or a reverse travel direction for the
follower vehicle based on a change in length of said tether.
CONTACTS
Autonomous Solutions, Inc.
990 North 8000 West
Mendon, UT 84325
General Inquiries
ASI Sales
Tel: 866.881.2171 x3
info@asirobots.com
Support Contact
ASI Support
Tel: 866.881.2171 x1141
support@asirobots.com
Website: http://www.asirobots.com
LINKS
& REFERENCE
http://www.ipo.gov.uk/ http://patft.uspto.gov/Robots+Guidance http://www.google.co.in/patents/US4769700 http://www.edisonawards.com http://www.trademarkia.com/guideline-robotic-convoy-85864421.html https://twitter.com/ASIRobots/status/329336621256298496 https://showyou.com/v/y-0pKeCxd04Aw/guideline-robotic-convoy-system http://www.robotxworld.com/asi-guideline-robotic-convoy-system-nominated-as-2013
https://www.facebook.com/video/video.php?v=124026484398947
http://www.edisonawards.com/
http://www.prweb.com/releases/2013/3/prweb10554855.htm
|