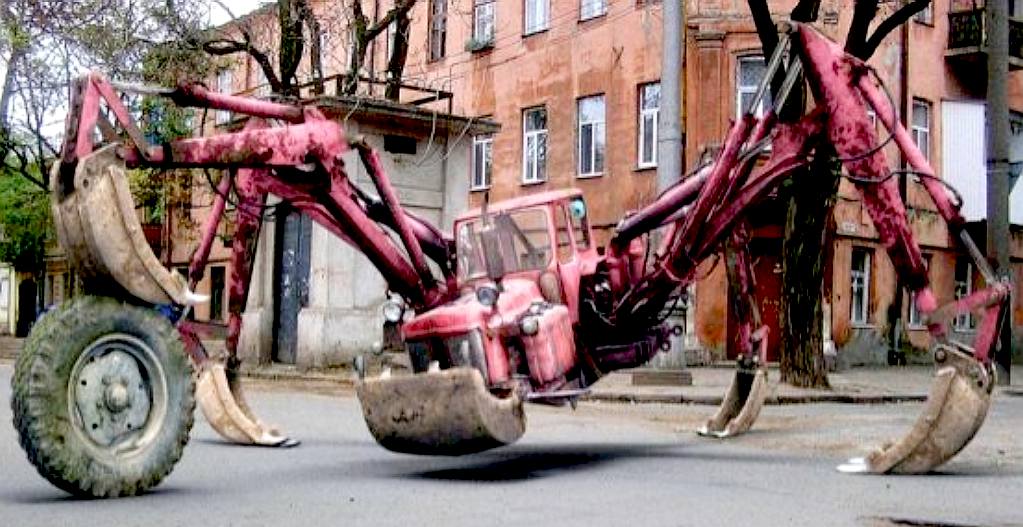
BOSTON
GLOBE JULY 16 2015
For the first time since they started the ambitious undertaking three years ago, members of Project Hexapod have recently taken their six-legged robot, Stompy, out of the workshop and into the sunshine.
The 10-person team hopes that within a few months it can complete its mission of having a human slip into the cockpit of the spider-like steel machine and take it for a spin.
“It will be a Stompy field day,” said Aaron Grossman, a mechanical engineer who is the project manager.
Once a week for the last three years, the team has convened at the Artisan’s Asylum in Somerville to work on the 6,000-pound robot, which stands on six hydraulic legs and is powered by a propane engine that was stripped from a forklift.
The group raised funds for the project through a Kickstarter campaign launched in 2012. The plea to help Project Hexapod realize their robotic vision apparently resonated with some people. The group amassed $98,000 from supporters, some of whom will have their names slapped on the side of the monstrous machine for their contributions.
“We just all felt that building giant robots was a thing that needed to happen,” Grossman said about creating Stompy.
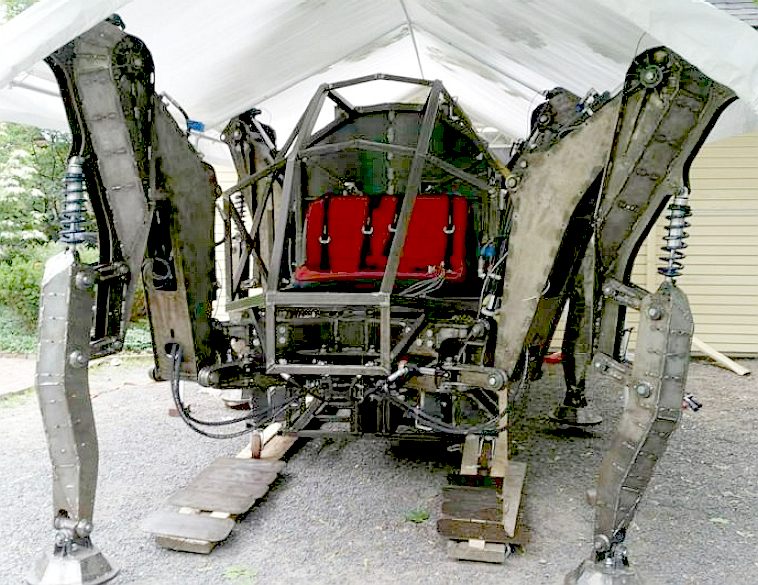
In April, Stompy moved under computer control for the first time. The team decided in late June to move the giant “mech” from the Somerville workshop as Stompy’s width grew to 18 feet — roughly the equivalent of a lane-and-a-half on the highway. After strapping it to a flatbed truck, they transported it to a team member’s driveway, stashing it under a carport for safekeeping.
Now, Grossman said, engineers and software developers are focusing on programming Stompy to stand on its own and eventually getting its legs to crawl forward at speeds of up to 3 miles per hour.
They have tested individual legs, but calibrating the entire system will take some work. Every leg has a computer in it to control that appendage.
“It has been a long time coming, but we are hitting a new stride,” said Grossman. “We’re really outside, and we really have this whole thing put together.”
The timeline for getting Stompy moving depends on a few factors, including the weather, but the goal is to have Stompy ready for public debut within four months.
“The world needs to have more giant robots,” Grossman said.
By
Steve Annear steve.annear@globe.com
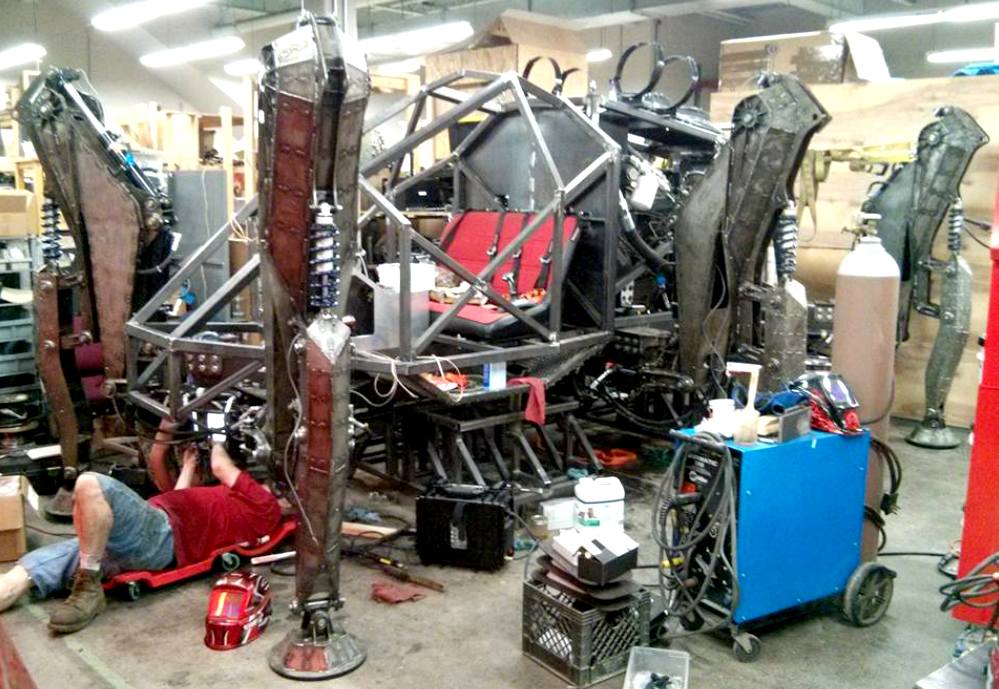
1 June 2015
-
A long week of pushing and the engine's brought up, propane tank mounts are attached, hydraulics are sealed and ready for the field, all sensors are mounted, wiring harnesses are ready for installation, and the control nodes are being flashed and prepared for installation. We have a single-spaced page's worth of items to check off before we take the robot outside for testing. Get ready, folks.
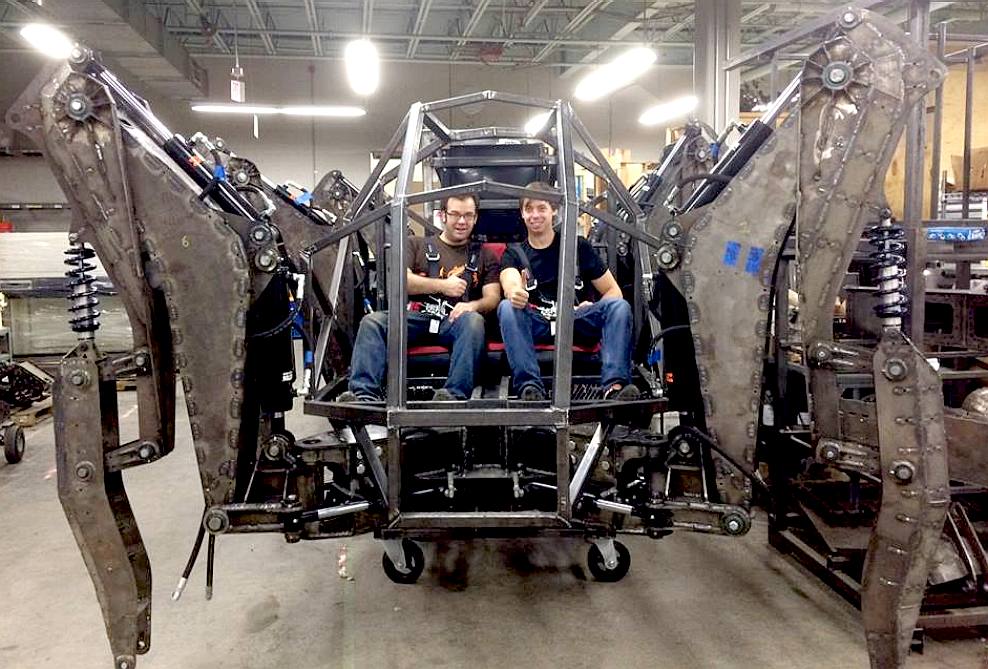
23 November 2014 -
It may not look like much, but today's big accomplishment was making sure every pin on the lower legs successfully assembled. There was a lot of clamping and bending metal by fractions of an inch, but by the end of the day, the lower leg pins and joints all went together!
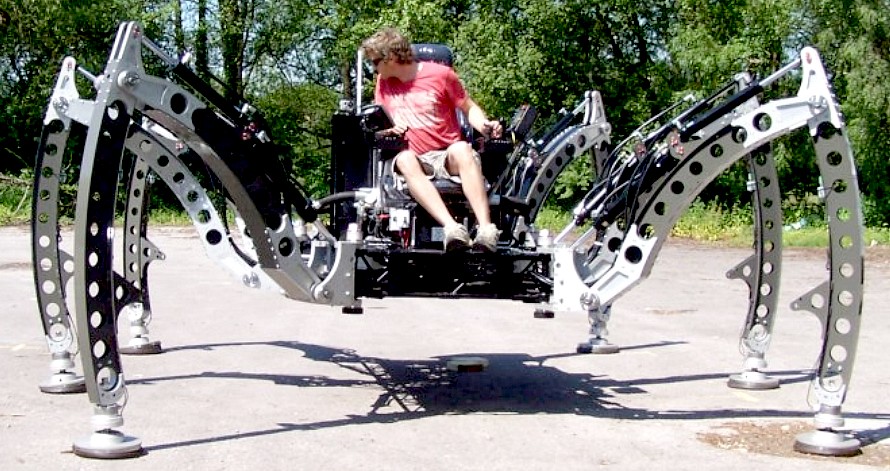
THE
MANTIS - Compare Stompy with Matt Denton's giant hexapod. Stompy
may be a little bigger and has two seats, otherwise, the concept is
similar. Matt Denton, from Hampshire, estimates his "very expensive toy" has cost him hundreds of thousands of pounds.
In April 2013 Matt told the BBC
that a mining company and a marine research organisation are now interested in his design and he hopes it might be used at science fairs.
During its development the machine had one outing, at a music festival, where Mr Denton says it was well received.
"It's an entertainment vehicle," he said in 2013. "But I hope it will inspire people."
The project was only initially intended to take 12 months, Mr Denton, who usually specialises in small-scale animatronics for the
film
industry, said. "After 18 months we tried the model out. We had to completely strip out and rebuild the legs. They were too heavy and complicated.
Image caption Animatronics expert Matt Denton says his machine's legs are inefficient.
"I'm a software and electronics engineer so this was out of my area - I had to learn fast."
The robot, driver-operated by joysticks within a cockpit, can only travel at 1.5km/h (1mph) and manage a distance of 5km on a 20-litre (4.5-gallon) tank of diesel.
"It's not about miles to the gallon, it's about gallons to the mile," he said.
"It wasn't built to be efficient and fast. It was built to look cool and insect-like and fun."
Mr Denton said he was inspired by science fiction to create the "walking" machine.
"But legs are very inefficient - the wheel was invented for a
reason."
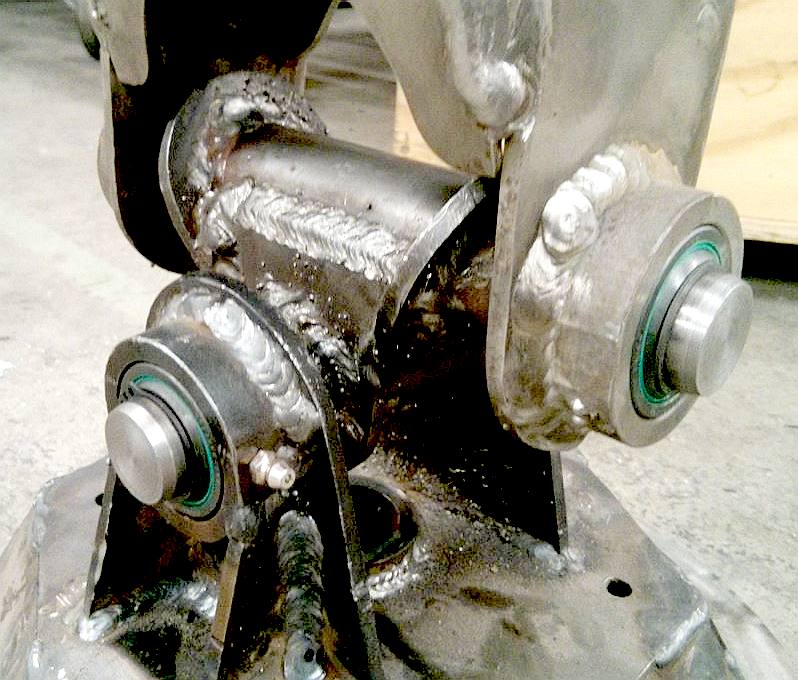
27 October 2014 -
The thigh actuator mounts on the hip didn't line up to the joint pin, so
they cut off one of the actuator mounts.
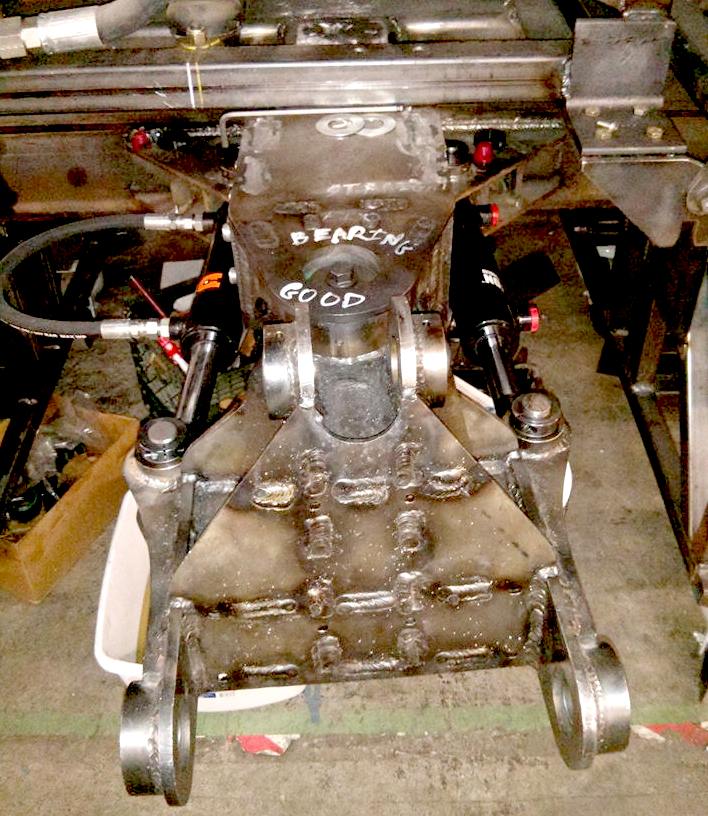
24 October 2014 -
As a result of several late nights in this week, the team were happy to report
that they have 5 thighs on. They ran into a welding distortion problem with the last hip and thigh, but
this was fixed on a Sunday to get the last thigh segment installed.
Praise the Lord.
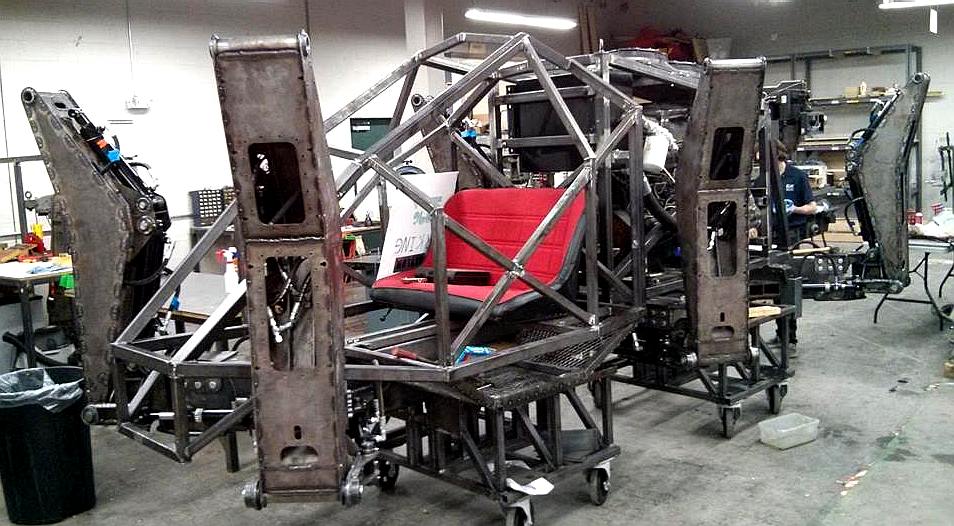
15 October 2014
-
All 6 hip linkages have been successfully installed on the robot, and actuators have been hooked up to each! This
means that they we're just about ready for final mechanical assembly of the legs onto the body of the
robot. There is though no body, just a steel cage around the occupants.
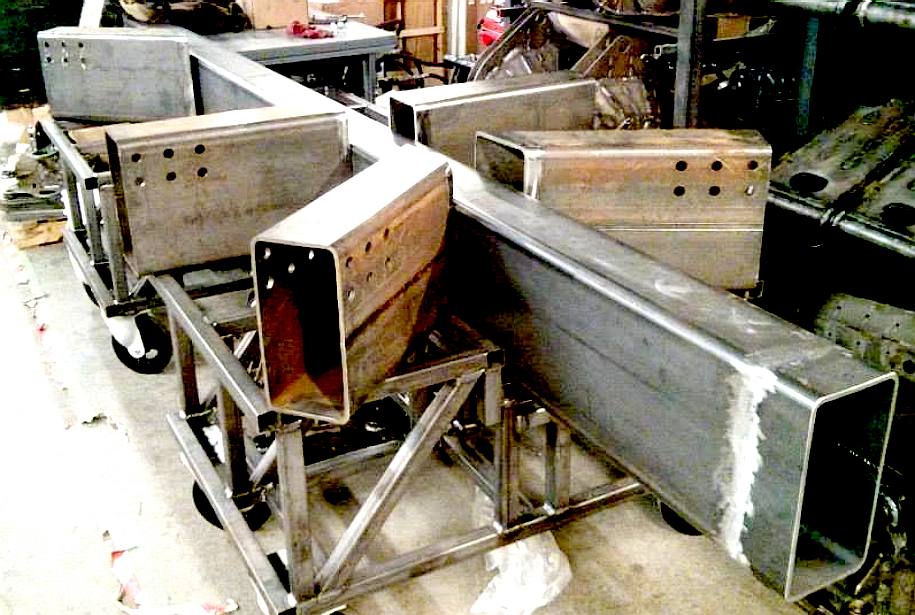
STOMPY
6 TON HEXAPOD PROJECT - Check out the frame of the main chassis section for
this US robot vehicle project. Strictly speaking this is not a robot, but
a machine driven by a human operator who sits inside a cab, much like
the Mantis hexapod project of Matt Denton, a few years back.
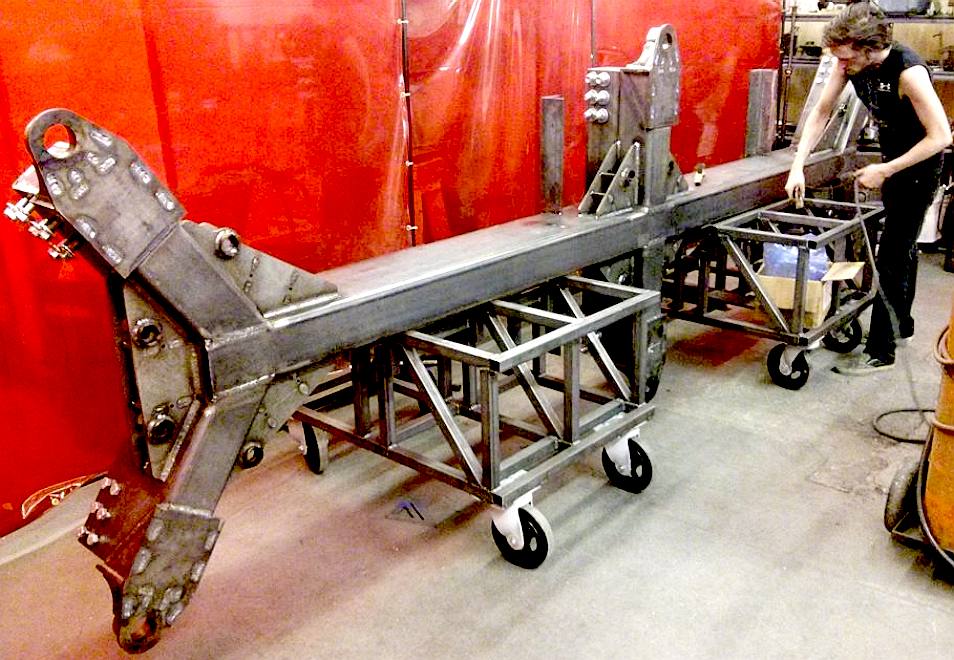
10 August 2014 -
By virtue of the number of spools of welding wire they'd gone through,
the team estimate that they put at least 200 pounds of steel on this robot between the legs,
power-plant, and chassis.
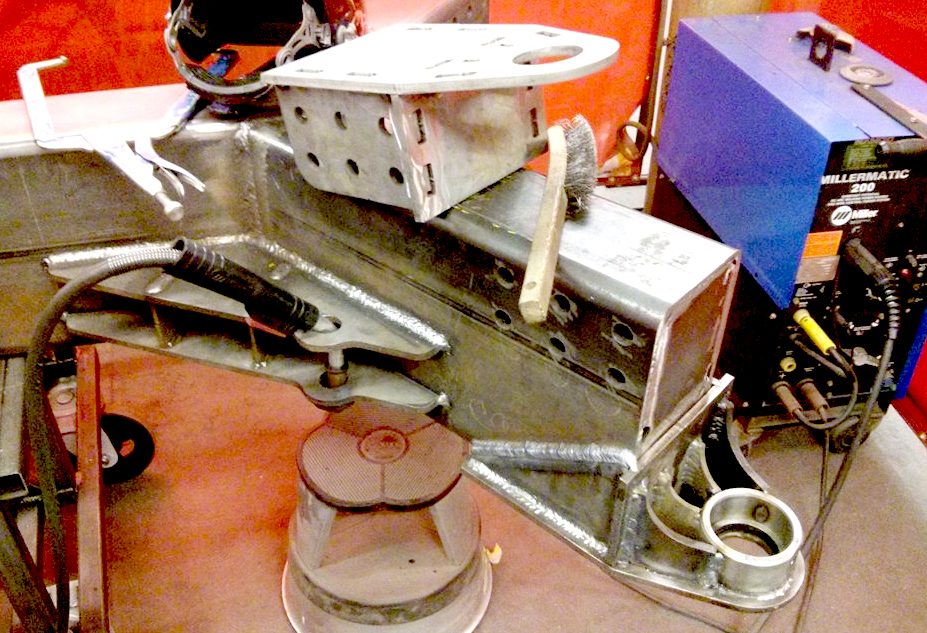
13 June 2014 -
A couple of legs were missing because they didn't go together just right the first time, so
the team took them apart and fixed them over the next seven days. Check
Next is to tear them all down again and install electronics and
hydraulics.
FUNDING
PERIOD: Aug 3, 2012 - Sep 2, 2012 (30 days) - RESULT:
1,571 Backers contributed $97,817 pledged of $65,000 goal = $32,817 dollars
generously oversubscribed. FUNDED! This project successfully raised its funding goal on Sep 2, 2012.
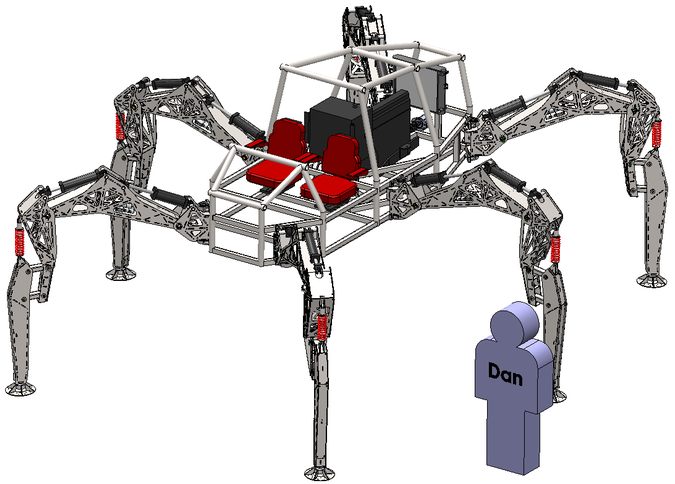
Meet
Stompy: An open-source, 18ft wide, 4,000 pound, 6-legged hydraulic robot that you can ride.
FUNDING
UPDATE: ALMOST TO FIRST UPGRADE PACKAGE!
Wow, we've reached $65,000 in 11 days! Thank you all so much for your support, this has been such an amazing ride so far! We want to take a quick moment to point out our next stretch goal - this is what will happen if we keep going:
At $95,000, we’ll drop in what we call the “Performance Upgrade”. We’ll integrate a number of new sensors that will let us more accurately detect and respond to rough terrain, allowing for a smooth ride over a much greater variety of terrain. We’ll upgrade our hydraulic powerplant to allow for a higher ground speed. We’ll also add sensors that will allow for some amount of autonomy, for future robot development.
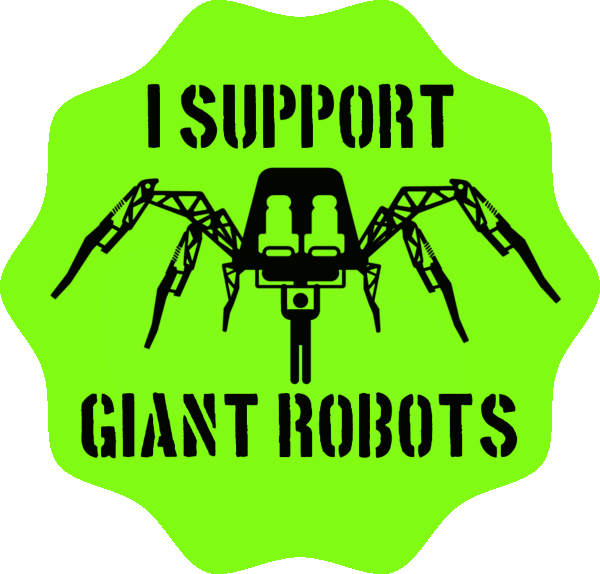
THE
DREAM
We dream of a world where imagination becomes reality simply because enough passionate people decide that an idea has merit. We dream of robots of all shapes and sizes being made across the globe, because the high-end technology needed to make them is simplified, generalized, and made publicly accessible.
The first step in achieving that dream for us is building a rideable, 18 foot wide, 4,000 pound, 6-legged, engine-powered hydraulic walking robot named Stompy, and sharing exactly how we did it with the world.
Who We Are
We are Project Hexapod. We’re a team of 3 instructors, 1 TA, and 15 students based out of a makerspace in Somerville, Massachusetts called Artisan’s Asylum. We’ve spent the last four months running a class on how to design giant robots, and Stompy is the end result. Our instructors (Gui Cavalcanti, James Whong, and Dan Cody) are professional roboticists who have designed military and commercial robot legs, arms, prosthetics, walking machines, and more. Our TA (Adam Bercu) is a national champion Battlebots builder, and our students come from backgrounds ranging as widely as engineers working for defense contractors to professional programmers to electronics enthusiasts.
You may have heard of us and Stompy before, a couple of months back – we were written up in Wired, Boing Boing, Hack A Day, DVICE, Hizook, the Boston Globe, and Engadget, among others.
Why You Should Care
First of all, we’re building a giant walking robot that you can ride, and if all goes according to plan, we’ll be showing it off at a festival or fair near you. Depending on your level of support, you may even get to ride it or drive it - how about that?
Beyond that, though, your support for Project Hexapod will drive a personal robotics revolution (if we have anything to say about it). The past twenty years have seen an explosion of productivity in hobbyist robotics made possible by cheap, easy to use microcontrollers and RC servos. The hobbyist community has built a wealth of knowledge and infrastructure around these components, but RC servos severely limit the size of robot you can build.
Project Hexapod wants to make large-scale robots easier to build, and inspire people to build them.
Stompy is 6 giant steps towards that dream. Once we finish this robot, we’re releasing our plans, our CAD, our diagrams, the presentations from all the lectures we gave in class, our lists of materials and parts, everything. The construction and control techniques we're using will drop the cost of controlled hydraulics by an order of magnitude or two from where they are now, and will make giant robots affordable to small groups of enthusiasts everywhere.
The robot isn't just being built for fun, though - it has incredibly practical purposes, as well. With 6 force-sensitive legs and a ground clearance of 6 feet, the robot will be able to walk over broken terrain that varies from mountainous areas, to rubble piles, to water up to 7 or 8 feet deep - everywhere existing ground vehicles can't go. Not only that, but while navigating such terrain, Stompy could carry 1,000 pounds at 2-3 mph, and up to 4,000 pounds at 1 mph. This is important because in disaster areas like Haiti's Port Au Prince, it's taken more than three years to clear the rubble out of some areas - meaning that throughout that entire time, people have had to be rescued or resupplied by helicopter, because no ground vehicle could reach them. Stompy (and the technology it represents) could easily reach people who can't be reached by any other means in a natural disaster.
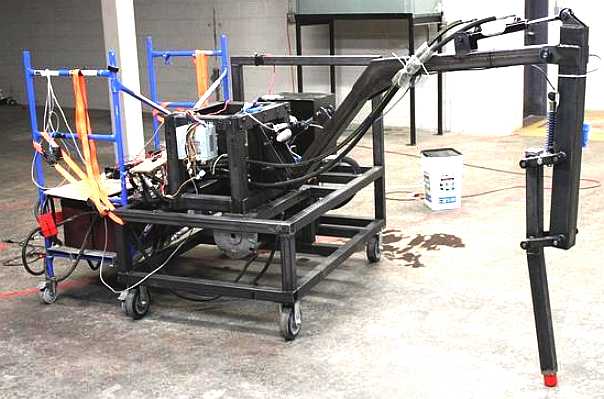
LEVELS OF SUPPORT AND WHAT YOU GET
We’re not your average Kickstarter campaign, so we don’t have your average Kickstarter levels. At a level of support of $100 or below, we’re going to shout your name from the top of the White Mountains, give you a ton of cool swag (designed by local artists Maria Stangel and Ecco Pierce), and list you as a supporter on our website. At the $10 level, that swag includes a bumper sticker proclaiming your desires for your other car:
The $20 level includes a robot apocalypse friendship bracelet that reads 'FRIEND OF ROBOTS - DO NOT TERMINATE'; wear it to ensure your safety during the upcoming robot revolution! At the $40 level, you get your choice of one of the following T-shirts:
At the $75 level, you'll get both shirts (or two of one, if you prefer). Feel free to add $35 to any pledge level to get an additional shirt!
Finally, at the $100 level, we'll send you a signed photo of the entire team in front of the finished Stompy, giving the camera cheesy thumbs ups! After the swag levels, though, things get…interesting.
At the $200 level, you get to choose between having 10 characters of your choice welded onto our chassis or supplying an inanimate object of your choice for Stompy to crush mercilessly. At the $300 level you get a ride, at the $1,000 level you get to drive, and at the $2,500 to $5,000 level you (or your company) get to be listed as a sponsor. At the $10,000 level we’ll fly you out to Boston for a weekend (if you’re in the lower 48 states – international supporters, call us beforehand!), give you free ice cream and burgers, and take field trips with Stompy to local rubble piles and scrap yards.
Contact us directly if you’re interested in higher levels; $25,000 will get you a Stompy appearance in the lower 48 states once the robot’s done, and $300,000 will get you another Stompy of your very own!
WHAT
WE'VE DONE SO FAR
Over
the past four months, we've...
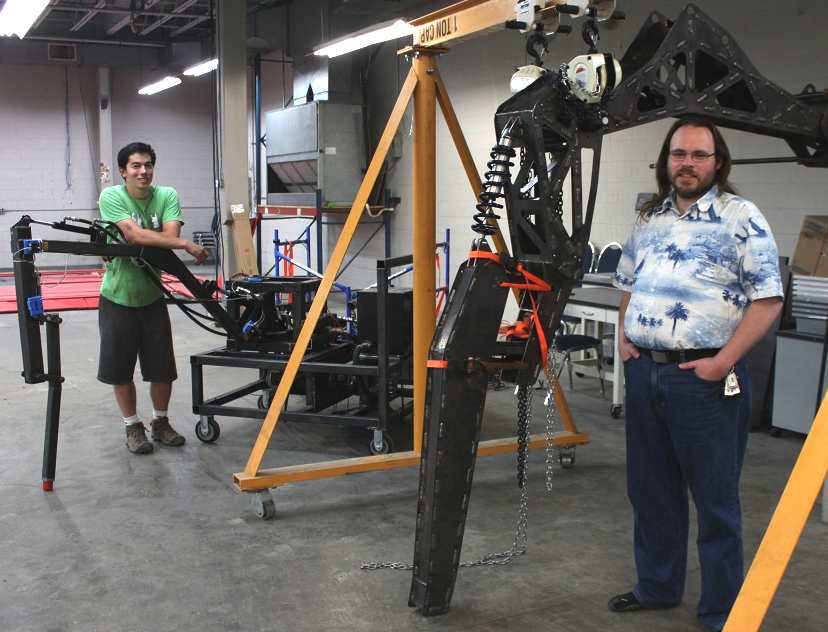
WHAT
WE'RE DOING NOW
Right now we’re building a full-scale prototype leg to make sure our design methodology, actuator sizing, and finite element analysis are all up to snuff before anyone sets foot in the actual robot. Once we establish that, we’ll be finishing the design of our chassis – at the end of our four week Kickstarter campaign, we expect we’ll be ready to press print on our drawings and start cutting and welding steel!
What We'll Do With The Money
We’re asking for a lot of money, and it’s all going straight into the hardware necessary to build the robot. We estimate that each leg will cost around $6,000, to cover the 350 pounds of waterjet-cut steel, high quality shock absorbers, three hydraulic cylinders, valves, sensors, and what have you. The body of the robot (which accounts for around 1,000 pounds of steel), consumables, electronics, and miscellaneous items like screws and wire make up the balance.
While $65,000 sounds like a lot of money for a project claiming to be low cost, bear in mind that an equivalent robot built with high-end technology could easily cost on the order of a couple of million dollars. As a point of reference, using our technology results in position-controlled hydraulic actuators that can produce 18,000 pounds of force, with strokes up to 2 feet in length... for all of $400 an axis. That's less than some hobby servos. Most of the cost of this project is in steel and other components.
Once we get the money, we'll order the thousands of pounds of steel, start the waterjet running at Excell Solutions (our contracted machine shop), and start welding everything together at Artisan's Asylum. We're budgeting 8 months to finish the robot, from the initial steel order.
Once we finish the robot, we’ll have a series of demo days and festivals where we give rides, let people drive, stomp things for fun, and more!
WHAT WE'LL DO WITH A LOT OF MONEY
We have big plans for what will happen if this takes off…
At $95,000, we’ll drop in what we call the “Performance Upgrade”. We’ll integrate a number of new sensors that will let us more accurately detect and respond to rough terrain, allowing for a smooth ride over a much greater variety of terrain. We’ll upgrade our hydraulic powerplant to allow for a higher ground speed. We’ll also add sensors that will allow for some amount of autonomy, for future robot development.
At $125,000, we’re going to install the “Flair Upgrade”. We’ll give Stompy an animatronic head, a killer paint job, a sound system, and (pending a full safety review of the robot once it’s built) flame effects.
At $300,000, we’re going to make this a Really Big Deal. We’re going to buy a waterjet cutter and install it at Artisan’s Asylum for public use, start a company devoted to creating open-source high-end robotic technology, and start developing a zoo’s worth of rideable robots. We’re not even kidding.
Any funding left over from the project will be put in a bank account and reserved for seed funding for future giant robot projects.
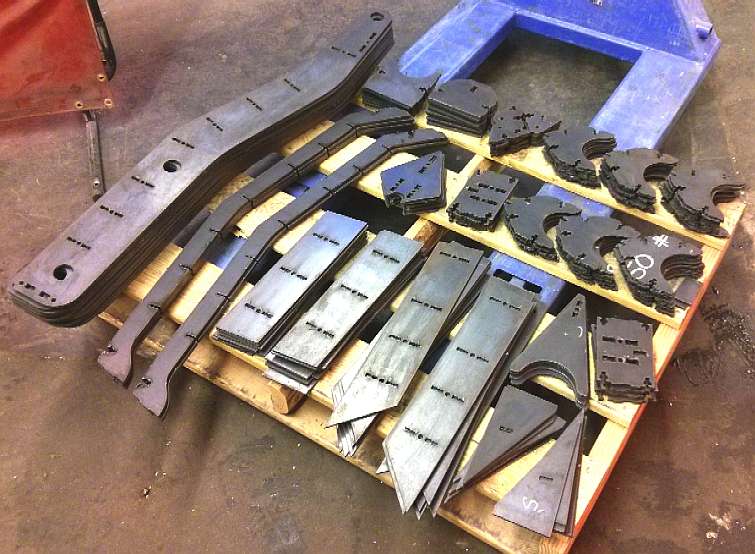
FREQUENTLY
ASKED QUESTIONS
Why are you waterjet cutting? Plasma is cheaper...
We chose waterjet because we're trying to come up with processes that involve the absolute least amount of setup and work. Waterjet on the first pass means we don't have to come back and do any secondary/post machining. To be clear, we don't have a waterjet ourselves, we're just shopping it out for now.
Last updated: Monday Aug 6, 1:54am EDT
Where and when will we get our rides/drives/etc?
Stompy is being built in Artisan's Asylum, which is located at 10 Tyler Street, Somerville MA. Our initial round of demo days will be in the Artisan's Asylum parking lot, which is adjacent to us. We'll be announcing the exact demo day dates at least a month or two in advance, and expect them to be mid-April to mid-May.
Last updated: Thursday Aug 9, 3:00pm EDT
How much do I need to add to my pledge to ship internationally?
We expect everything below the $100 level to ship for around $10 to $20 more. Please use the "International Small Flat Rate Box" option on the US Post Price Calculator
(http://ircalc.usps.gov/Default.aspx) to calculate how much you need to add to your pledge for shipping for a T-shirt, and the "International Small Flat Rate Envelope" for the wristband/sticker/etc.
Last updated: Thursday Aug 9, 3:00pm EDT
What's the difference between Stompy and art projects like the MondoSpider, Walking Beast, etc.?
Most of the art-based walking vehicles out there use reciprocating legs tied to a crank shaft to walk. This means they like walking in straight lines, or turning in place, but otherwise behave very similarly to a zero-turn-radius lawnmower. These vehicles are restricted to very flat terrain like the playa as a result. Because Stompy has fully independent control of 6 legs, it can walk sideways, turn in arcs, and walk over extremely rough and broken terrain, as it has the ability to sense the ground with each footstep.
Last updated: Thursday Aug 9, 3:00pm EDT
What's the difference between Stompy and industrial/military robots like the John Deere Timberjack, the OSU Adaptive Suspension vehicle, etc.?
Those machines are extremely expensive and generally closed source. What is open source is way out of the range of anything a hobbyist could pull off - all of them require extremely precise engineering and design. Stompy is on the order of 1/10 the price of either, open source, extremely simple, and (fingers crossed) just as capable.
Last updated: Thursday Aug 9, 3:00pm EDT
Can you make a small Stompy that we can buy?
Kind of? Legs scale very strangely - at Stompy's scale, his actuators are less than 1/4 of the weight of the leg, and are on the order of 1/10 the volume. Translating the "look" of Stompy to a smaller robot is very hard, as weight and actuator power scales funny with length as you get small. Servo-based robots have legs that are primarily made of... well... servos, with some tiny bits of metal or plastic holding them together. We'll definitely take a look at what it would take to make a scaled-down model robot, but we want to make sure we can build the big one first!
Last updated: Thursday Aug 9, 3:00pm EDT
Can I come see Stompy being built?
Absolutely. Artisan's Asylum is a public workshop, and you should come check us out over the next few months as we build Stompy. Artisan's Asylum is at 10 Tyler Street, Somerville MA, and is open from noon until 8PM. We'll be announcing the demo days publicly, so that others can come check out the robot while it's running.
Last updated: Thursday Aug 9, 5:24pm EDT
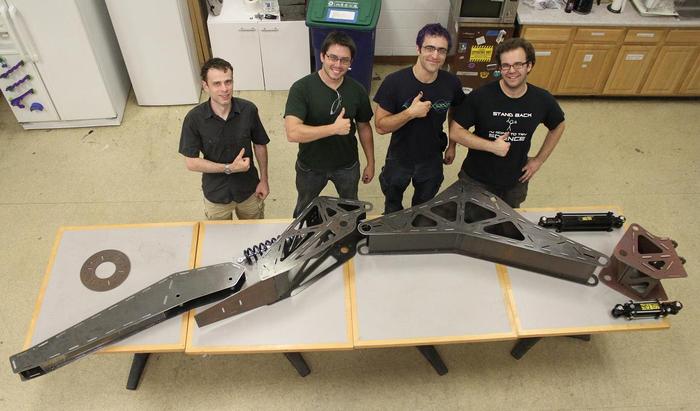
THE
DEALS
Pledge $5 or more
- 135 backers
The Project Hexapod team will take a field trip to the White Mountains, scale them, and shout your name from the top.
Estimated delivery: Sep 2012
Pledge $10 or more - 264 backers
A snazzy "My Other Car Has 6 Legs" bumper sticker, the listing of your name on our web site as a supporter, and the shouting of your name from a mountaintop.
Estimated delivery: Oct 2012
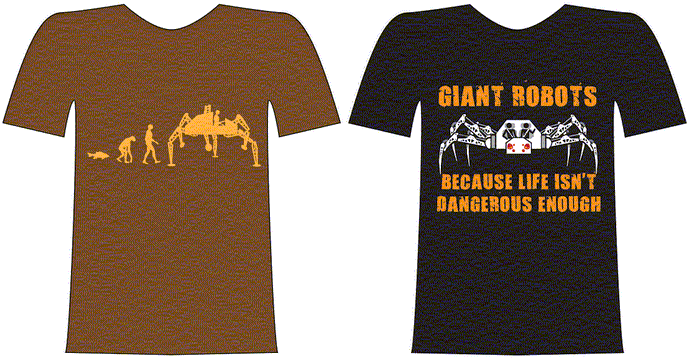
Pledge $20 or more - 324 backers
A wristband proclaiming "FRIEND OF ROBOTS - DO NOT TERMINATE" that clearly indicates your loyalties in the coming robot apocalypse. Oh, and the sticker, name on our website, and shout-out from the top of a mountain.
Estimated delivery: Oct 2012
Pledge $40 or more
- 488 backers
Our stylish Robot Evolution supporter T-shirt, plus the loyalty band, the sticker, your name on our website, and the mountain shout.
Estimated delivery: Oct 2012
Pledge $75 or more - 64 backers
You get two shirts! Whether they're both of one type, or one of each type, they are both yours. You also get the loyalty band, the sticker, your name on our website, and the mountain shout.
Estimated delivery: Oct 2012
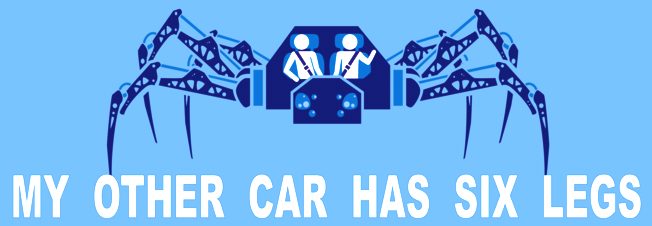
Pledge $100 or more - 65 backers
A signed photo of the Project Hexapod team standing in front of Stompy giving cheesy thumbs-ups, a T-shirt, the protective wristband, a sticker, your name on our website, and the shout-out.
Estimated delivery: Apr 2013
Pledge $200 or more - 14 backers
10 characters of your choosing (and our approval) are welded onto the chassis of Stompy, and we'll send you a picture. On top of that, you get the signed picture, T-shirt, band, sticker, name on our website, and shouting.
Estimated delivery: Apr 2013
Pledge $200 or more - 6 backers
WILL IT STOMP?! You get to provide us with an inanimate, non-volatile object of your choice (and our approval) and Stompy will crush it mercilessly. We will then post a video of the crushing on YouTube and set it to techno or some such. You also get the cheesy picture, T-shirt, loyalty wristband, sticker, name on our website, and shouting-from-the-mountaintop.
Estimated delivery: Apr 2013
Pledge $300 or more - 43 backers
You gave us $300? Whoa. You, dear friend, get to ride Stompy on one of our demo days. We suggest dressing up in your finest clothes, because this is going to be a grand celebration! We'll also get you the thumbs-up picture, the T-shirt, the sticker, the wristband, your name on our website, and the shouting.
Estimated delivery: May 2013
Pledge $400 or more - 1 backer
You're not satisfied with just a ride - you want both a ride, and the chance to either stomp something or write your name on the chassis in metal. Sounds good! At this level, you'll get both a ride and your choice of the $200 levels.
Estimated delivery: Apr 2013
Pledge $1,000 or more - 16 backers
Rides? Who needs rides. You certainly don't! You get to DRIVE Stompy on one of our demo days. We'll even throw in a training class beforehand! We strongly suggest a mad scientist look for the occasion - a good lab coat is almost required. You'll also get, of course, the cheesy photo, the Evolution T-shirt, the wristband, the sticker, your name on our website, and the shouting. Oh, the shouting.
Estimated delivery: May 2013
Pledge $1,500 or more - 2 backers
You're awesome. You know that? You're so awesome we're going to give you a chunk of our robot - no, you keep it. You earned it. At this level, we'll send you a signed thigh side plate that you can mount to your wall. We'll even give you a ride. We'll throw in the signed photo (which you could even hang by the thigh piece for context!), the T-shirt, the wristband, the sticker, your name on our website, and, of course, a shout-out. Except you know what? Your name will be shouted louder. That's right.
Estimated delivery: May 2013
Pledge $2,500 or more - 1 backer
Hang on... give us a moment... OK, we've collected ourselves. Congratulations! You've reached our sponsor level! You get an A4-sized logo on the robot's chassis - it'll be like NASCAR, only two orders of magnitude slower! We'll also throw in a ride, the picture, the shirt, the wristband, and the sticker. You'll be listed on our website as a sponsor instead of a supporter, and we'll be screaming your name from that mountain.
Estimated delivery: May 2013
Pledge $5,000 or more - 3 backers Limited (3 left of 6)
You know those Adopt-A-Highway programs? Well, you've just adopted a leg. That's right. Not only do you get your sponsor logo on the thigh of the leg in question, but you get to design a round logo that the foot will stomp into the ground on every step. We'll give you a ride, the picture, the shirt, the wristband, and the sticker. You'll be listed on our website as a sponsor, and everyone will be screaming your name in unison with a wild look in their eyes.
Estimated delivery: May 2013
Pledge $10,000 or more - 0 backers Limited (5 left of 5)
Uh. Hang on. Give us a minute. You know what? For this amount of money, we'll fly you to Boston (lower 48 states only!), put you up in a hotel room, and take you out on field trips to run Stompy through local rubble piles, scrap yards, and the like. We'll even throw in a free ice cream from J.P. Lick's and a trip to Bartley's Burgers. We'll give you the picture, the T-shirt, the wristband, and the sticker. You'll be listed as a sponsor on our website, and we'll be shouting your name 'till we're hoarse. Please contact us directly at
info@projecthexapod.com to arrange the details of this level.
Estimated delivery: Jun 2013
UPDATE
AUGUST 2013
Hi everyone!
It's been a long time since our last update, and we wanted to let you all know what's been going on. To make a long story short, we've moved out of our design and prototyping phase and into our build phase! Now that we're fabricating, we've decided to expand the team to include new skilled steel fabricators; if you're in the Boston area and are interested in joining us, check out the call for new members at the bottom of this update, or check out the application survey. Now, on to updates!
At the start of the year, we worked pretty hard to build out both the hydraulic powerplant for the final robot and a CNC Plasma Cutter (that would then be used to cut parts out for the robot's legs and chassis). Both items took us
a while to complete, and took more energy than we were hoping, but we wrapped them up around May. Since then, we've been working hard to finalize our leg design, get the links analyzed for overall strength and manufacturability, and create manufacturing and quality control processes from scratch to ensure that we build as robust a robot as we can. If you're interested, you can check out an example of the kinds of work instructions and processes we're creating here.
We're happy to announce that we've taken on two new sponsors recently, which have drastically helped our design and process; the first was Tompkins Industries, a global hydraulic fitting and hose supplier. We worked with them to design and supply custom hose assemblies and hydraulic fittings for all of the parts in the hydraulic powerplant, and will soon be working with them again to design the hose runs and fittings for the legs of the robot. The second sponsor was AST Bearings, a global supplier of bearings and bushings of all different shapes and sizes. We were having a lot of trouble coming up with cost-effective ways of designing and fabricating joints with rigid bushing assemblies that had to be concentric across big weldments made up of a lot of individual thin plates; in order to solve that fabrication problem, we worked with AST Bearings to source low-cost spherical plain bushings for all of our joints, meaning that Stompy will be much easier to weld together (for both us and any novice fabricators that follow in our footsteps), will be much easier to assemble in the short term, and will require less maintenance in the long run.
As we mentioned above, we're now solidly in the build phase of the project. We've decided to start by building the lowest-stress parts of the leg first in order to get all of our fabricators on the same page; we're building the "calf" link, as we call it. This is the link that touches the ground, and is suspended from the rest of the leg via a four-bar linkage and shock absorber. This is what 8 calves (one to screw up, one for a 'spare' leg, and 6 to put on the robot) worth of parts look like when the parts come out of the CNC Plasma Cutter:
All 184 of those calf parts have to have dross removed from them, and they have to be ground down and cleaned wherever we plan on welding so that we don't get contaminated welds. We expect that the legs represent at least 1,100 person-hours worth of fabrication, all told, without including assembly onto the robot itself or building the chassis. Needless to say, there's a tremendous amount of work ahead of us, and we've decided to ask for help to get it all done in a reasonable amount of time.
If you're in the Boston area, have experience with steel fabrication, and would like to join Project Hexapod, we'd love to hear from you! We're looking for somewhere between 4 and 8 new team members who can step up and help us build this giant robot over the coming months. If you're interested in learning more, please check out our application for new team members here:
http://www.surveymonkey.com/s/W23NKBD.
That's about it for now! We'll be posting lots of pictures of our build process to our Facebook page if you want to follow us there, and we'll be updating our blog soon with discoveries we've made during the build process.
Thanks everyone!
COMMENTS
Dennis G. Dahl on August 14
Your answer is good.
I'd not thought about the weight issue which is very valid.
Do you have anything like a mini prototype to sort out controls and guidance? There is a lot of this already going on and sourcing skilled folks to work on this should not be a problem.
Licensing, insurance and where to drive may end up being the biggest headaches.
Ever since I saw backhoes as a kid I dreamed of having a walking machine.
Keep at it!
Project Hexapod on August 14
Dennis - that's a good question. The primary driver was weight and manufacturability - an excavator boom from a similarly-sized construction vehicle weighs around an order of magnitude more than our existing legs. Our legs right now weigh around 400 pounds each, and those booms can easily reach 5,000 pounds on small excavators (since they build their castings with 1"+ wall thickness cast iron), and 10,000 to 20,000 pounds on medium-size machines. Quite simply, we have no way to work with metal that heavy - whether we're talking about lifting it, moving it, or modifying it. Also, once you have legs that weigh that much, the body has to weigh proportionally more so that the vehicle doesn't get rocked severely from the inertia of the legs moving from side to side. Overall, instead of the robot weighing 4,000 to 5,000 pounds, the robot would likely weigh on the order of 30,000 to 40,000 pounds.
We did investigate this option at the start of the project. Past the weight problem, we also ran into the problem of simply sourcing 6 identical digger arms - no used lot had 6 of the same exact machine, and no dealer would talk to us about just purchasing that one section of machine.
As far as getting to leg sequencing and control software, that's one of the first things we did immediately after the Kickstarter campaign, by building out the full-scale prototype leg. You can see a review of our efforts on controlling a single leg here: http://projecthexapod.com/blog/update-5212013/ and videos of the simulation we've been using to work on leg sequencing were actually included in the Kickstarter video itself - we've had them for quite some time. The legs themselves are actually mechanically designed to not interfere with each other's range of motion.
Thanks for the note!
Dennis G. Dahl on August 14
Guys, I'm really sorry to ask this again but why did you not choose to build using 6 backhoes? At least for a full scale prototype to help debug the controls.
I'm not against what you are doing but in my opinion you would have had a full size prototype up and running a lot faster with those sorts of "off the shelf" parts. Instead you are still cutting metal.
Was it cost prohibitive?
I do see you enjoy the learning experience but when will you get to the proportional hydraulic valve sequencing, motion clash prevention software and proximity detection for individual leg placement, etc.?
I feel qualified to ask because I have been designing instrumentation for the energy business for 34 years.
Dennis G Dahl, C.Tech.
Email: Withdrawn
Home address:
Calgary, AB Canada
Phone: Withdrawn
Bluebird
Marine Systems September 7 2013 - Update December 2015
Guys,
absolutely splendid project. We followed Matt Denton's "Mantis"
project in the UK, which is not a million miles away from your own.
There is of course huge scope for improving speed and other design
parameters to make such a vehicle useful in practical terms.
Not
to pour cold water, but Matt started out small then built his superb
full size creation, capable of around 2 miles per hour. We anticipate
that your vehicle will be faster and more agile? Matt's genius is
programming for lifelike mobility. Do you guys talk?
As
to the very valid comments on backhoes from Dennis, Matt thought about
going that route in the early days hoping to attract sponsors. We're
unsure if that helped Matt's cause, but clearly he custom built in the
end.
We
are building a 1/20th model of a full size robot
ship - to iron out the kinks - based on significant theoretical
performance improvements for solar boats - as in power to weight ratios.
We were thinking of doing a Kickstarter launch ourselves in the coming
year, but for the boat that is out of the question. Robots rule!
Keep
up the good work and very best of luck from all of us here in the UK.
Leslie
BMS
Ltd
SPONSORS
http://www.astbearings.com/
http://www.tompkinsind.com/
LINKS
& REFERENCE
http://www.tompkinsind.com/ http://www.astbearings.com/
http://www.kickstarter.com/projects/projecthexapod/stompy-the-giant-rideable-walking-robot-0
http://www.kickstarter.com/projects/robotboat/robotboat-mark-vi http://www.militaryaerospace.com/articles/2013/07/darpa-uuv-mothership.html
http://nosint.blogspot.co.uk/2013/07/darpa-considers-unmanned-submersible.html
https://www.facebook.com/ProjectHexapod/
steve.annear@globe.com
https://twitter.com/mantisrobot
http://www.bbc.co.uk/news/technology-22231365
Facebook
Project Hexapod
http://airsoc.com/articles/view/id/51f6a7809aad9d6f20000002/darpa-hydra-unmanned-submarine-to-deploy-drones#.Uhfr1NKsg6Y
http://en.wikipedia.org/wiki/DARPA
http://www.darpa.mil/
http://www.science.mod.uk/Engagement/the_portal.aspx http://www.science.mod.uk/Engagement/enterprise.aspx https://www.dstl.gov.uk/centrefordefenceenterprise https://www.dstl.gov.uk
UKHO
http://www.maritimejournal.com/news101/industry-news/ukho-appoints-new-national-hydrographer http://en.wikipedia.org/wiki/United_Kingdom_Hydrographic_Office http://www.ths.org.uk http://www.spri.cam.ac.uk/friends/committee/ http://www.thefutureofnavigation.com/ten_steps.aspx
https://www.dstl.gov.uk/insight
US
Department of Navy Research, development & Acquisition - http://acquisition.navy.mil/ US
Fleet Forces Command - http://www.cffc.navy.mil/
US
http://www.msc.navy.mil/
Kickstarter
robotboat mark vi projecti
http://www.kickstarter.com/projects/projecthexapod/stompy-the-giant-rideable-walking-robot-0/posts/568632
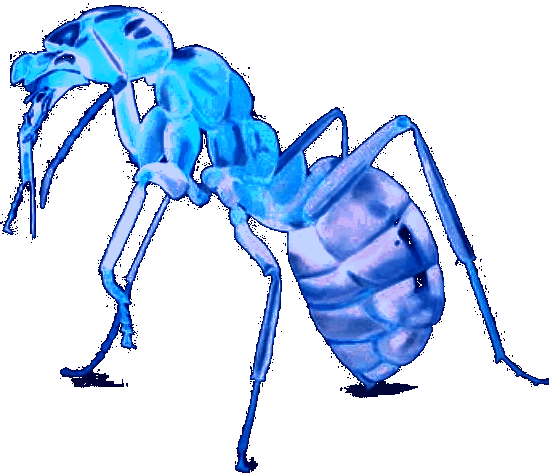
ROBOTS
- Extend the ability of humans to do things and go places that would not
have been possible only 50 years ago. As robots improve the potential for
a brighter human future will blossom. Robots will only improve as humans
work together to develop them.
|