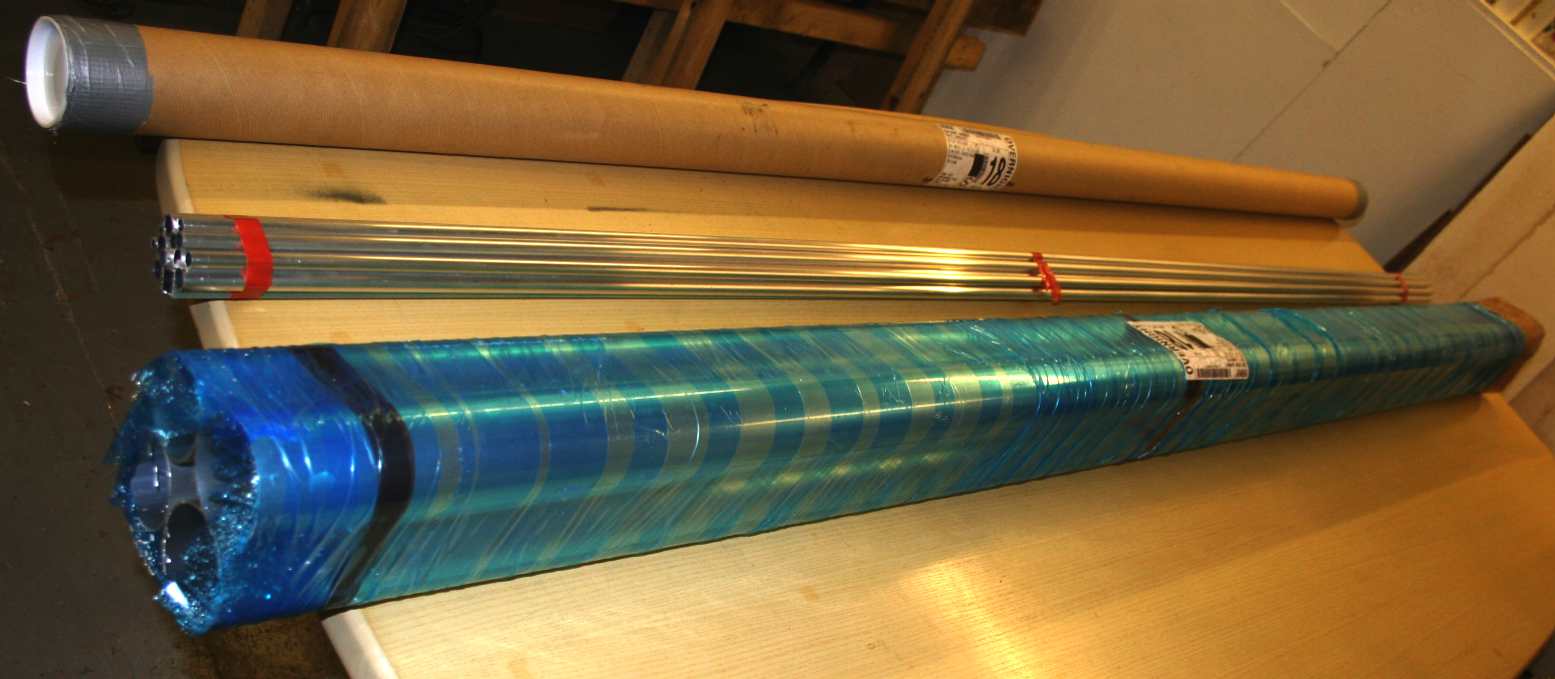
High
quality aluminium demands high quality packaging. Aluminium Warehouse did us
proud. The 16g medium diameter tubing was supplied as shown, with the smaller
and one longer 5.0m length tube (not shown) coming in the cardboard tubes. The
1mm sheet alloy (not shown) was also protectively sandwiched between two 8' x
4' timber pallets. Apart from the expense of the pallets, AWs products are
great value for money. When ordering sheet, buy as much as you need for
forward works, to spread the pallet cost.
ALUMINIUM
AS A BOAT BUILDING MATERIAL We've
now got a solid Jig to work from. The full size vessel will be built of 5383
alloy, commonly known as Sealium, from Pechiney (the inventors). The models we
are fabricating are to be built from more modest alloys, because they do not
have ten years of life at sea ahead of them - and we are on a tight
budget. DEVELOPMENT Though
we are building an advanced robot ship, you may have noticed that the model
development has been almost exclusively hand crafted. Yes, okay, from computer
generated drawings, but those in turn came from hand drawings. The boat building
craft is still alive. Having said that, the full size vessel will more than
likely be assembled from a water-jet cut list of parts. On the other hand,
construction at this scale is a useful dry run that will mean that this design
could be built in any reasonably equipped boat yard anywhere in the world. As
the aluminium developments are cut and shaped, we will include them on this
page. At the moment we are converting the computer drawings to 1/20th scale
loftings. We are also test folding the developments in paper, before committing
to cutting any aluminium - as you can see from the pictures below. If it works
in paper it will work in aluminium. We have budgeted for only four sheets of 2m
x 1m aluminium, which is for three models. It is going to be tight.
She
is starting to look like the 1/200th model. We hope the envelope includes a
return address in case the open water trials go haywire. Many of the
Microtransat teams will (we hope) see the funny side of this. We are identifying
minor practical improvements to the jig as we go. It is very rewarding watching
an idea come to life from the drawing board - and we still use a conventional A1
drawing board. We also have an A0 size unit that stays tucked away because it is
too big for our modest workshops.
The
development would have been better using a thick cartridge paper, or heavy duty
lining paper. We didn't have the time to go shopping or wait for online
deliveries. So we used what was lying about in the office, including recycling
old envelopes and cardboard boxes. This picture shows the tucks for the port
side window frames. These are important for joining and must overlap internally
with sufficient width for either riveting or welding. A common mistake is not
including a return - which can make production difficult. A suitable return also
reinforces joins, apart from making the assembly process more idiot proof - and
we need plenty of that.
Sorry
about the poor quality of this picture, but it shows the starboard side window
tucked and folded nicely with returns that are deep enough to make pop riveting
an option. Masking tape that is not too sticky, is ideal for when the unfolding
process begins. Have a sharp Stanley knife to hand, just in case.
From
the folding of the paper development, fine adjustments to the cuts are noted and
incorporated for future reference. It's a bit like assembling a kitchen
flatpack. The first one takes more time as you figure out the assembly sequence.
For example, the folds on the window frames worked better at a slightly
different angle to that envisaged in the design drawings.
LEG
|
NAUTICAL
MILES
|
TIME
IN PORT
|
WAYPOINT
|
SUNSHINE
DAYS
|
-
|
-
|
-
|
-
|
-
|
|
-
|
-
|
Monaco
|
0.00
|
1
|
784
|
2
|
Gibraltar
|
4.67
|
2
|
729
|
2
|
Tenerife,
Canary Islands
|
4.34
|
3
|
3,154
|
2
|
Trinidad,
Port of Spain
|
18.77
|
4
|
1,182
|
2
|
Panama
City
|
7.04
|
5
|
970
|
2
|
Galapagos
|
5.77
|
6
|
3,640
|
2
|
Tahiti
|
21.67
|
7
|
1,423
|
2
|
Tonga,
Nukualofa
|
8.47
|
8
|
410
|
2
|
Fiji,
Suva
|
2.44
|
9
|
1,886
|
2
|
Port
Moresby PNG
|
11.23
|
10
|
340
|
2
|
Thursday
Island, Cape York
|
2.02
|
11
|
724
|
2
|
Darwin
|
4.31
|
12
|
1,572
|
2
|
Jakarta,
Indonesia
|
9.36
|
13
|
1,881
|
2
|
Colombo,
Sri Lanka
|
11.20
|
14
|
2,109
|
2
|
Aden,
Yemen
|
12.55
|
15
|
698
|
2
|
Jeddah,
Saudi Arabia
|
4.15
|
16
|
670
|
2
|
Port
Said, Egypt
|
3.99
|
17
|
1,111
|
2
|
Palermo,
Sicily
|
6.61
|
18
|
170
|
2
|
Naples,
Italy
|
1.01
|
19
|
393
|
|
Monaco
|
2.34
|
-
|
-
|
-
|
-
|
-
|
-
|
23,846
|
36
|
RUNTIME
DAYS @ 7kts
|
141.94
|
-
|
-
|
-
|
-
|
-
|
+
10% service
|
=
156.13 Days
|
-
|
7
KNOTS AVE INC PORT & %
|
192.13
|
-&
maintenance
|
-
|
-
|
AT
6 KNOTS AVE
|
224.16
|
-
|
-
|
-
|
AT
5 KNOTS AVE
|
268.99
|
TRANSIT
EXAMPLES - The above table illustrates one of the most likely
ocean awareness expedition routes that could be undertaken by the Elizabeth
Swan, showing the time elapsed in days for 7 knots average cruising
speed, including times for 5 and 6 knot averages - allowing for 10%
downtime and 36 days in ports. Hence, although the objective is to reduce
the current solar circumnavigation record from 584 days, the event in not
an outright non-stop yacht competition in the offshore racing sense. It
remains to be seen how accurate such a prediction might be.
The
distance between submerged hull and helm superstructure determines the performance
of the full size vessel in heavy seas. The next development is the fore and aft
foils. These are very important and must have just the right amount of reserve buoyancy
to keep the hulls running true. Too much buoyancy and the SWASH
hull qualities are lessened. That is of course a design compromise - better
tested at this scale when modifications are not that expensive. Yes, we've
learned the hard way.
A
design of this caliber deserves a suitably sculptured figure head. The Solar
Lady will adorn the full size vessel at somewhere between 2.5 and 5.0 meters.
The mermaid inspired carving shown here would be 5.1 meters on the full size
craft. Weight is a consideration. The Solar Lady sculpture is far to valuable to
include for model tank and open water testing .
To
make the foils we begin by shaping up some solid timber to make a wooden buck.
Over this former we can then bend aluminium sheet blanks to make as many foils
as we want, all to the same section. This is important where we are making
several versions of the same hull, a civilian survey vessel and a couple of
military concepts, to include a micro-battleship
and a mini aircraft
carrier that carries a squadron of drone quadcopters.
JOINING
ALUMINIUM We
will be using a combination of alloy welding/brazing - and pop riveting to make
these test models. The full size robot ship will be mostly MIG and TIG welded.
Fortunately, for the proposed Kickstarter project in 2015, one of our in-house
boat builders is a skilled welder.
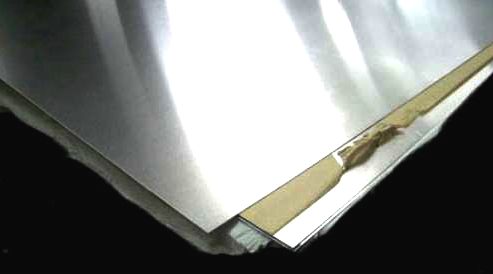
Aluminium
raw materials 6063T6 and 5251 H22 grades ordered June 21st 2013 from Aluminium
Warehouse, which company offers a friendly, efficient service within the United
Kingdom, and simply superb packaging as you can see for yourselves:
F.
COSTING ESTIMATES ALLY FOR R/C MODEL ACTIVE HULL BUILD @ 1/20TH SCALE
|
4 |
2000
mm x 1000 mm x 1.0 mm - 5251 H22 - Standard mill finish |
£18.60
|
£74.40
|
2 |
Aluminium
Round Tube (6063T6) 21/2 in x 16 swg -
2500 mm |
£
9.76
|
£19.52
|
1 |
Aluminium
Square Tube (6063T6) 3/4 in x 3/4
in x 16 swg - 2500 mm |
£
3.63
|
£
3.63
|
5 |
Aluminium
Round Tube (6063T6) 1/2 in x 18 swg - 2500
mm |
£
1.72
|
£
8.60
|
1 |
Aluminium
Round Tube (6082T6) 23/4 in x 16 swg -
5000 mm |
£22.72
|
£22.72
|
2 |
Aluminium
Round Tube (6063T6) 3 in x 16 swg - 2500 mm |
£12.49
|
£24.97
|
2 |
Aluminium
Round Tube (6063T6) 3/8 in x 16 swg - 2000
mm |
£
2.40
|
£
4.80
|
5 |
Aluminium
Round Tube (6063T6) 5/8 in x 18 swg - 2500
mm |
£
2.80
|
£14.00
|
|
Sub-Total
(ex VAT): |
 |
£172.65
|
Price
Break Discount (ex VAT): |
 |
-
£ 8.63
|
Sheet
Metal Shipping Rate (ex VAT): |
 |
£
49.90
|
UK
VAT 20.0%: |
 |
£
42.78
|
Total: |
 |
£256.70
|
K.
COSTING ESTIMATES
FOR R/C MODEL ACTIVE HULL BUILD @ 1/20TH SCALE
. |
Heating |
. |
300 |
Power
& lights |
. |
200 |
Labour:
fabrication |
.26
weeks |
13,000 |
Tank
and open water testing |
.4
weeks |
2000 |
Insurance |
. |
600 |
. |
. |
. |
Mothership
build |
Sub
Total |
£
15,500 |
. |
. |
. |
Contingency |
@
35% |
£
5,425 |
. |
. |
. |
. |
Build Total |
£ 20,925 |
BLUEFISH:
BLUEBIRD
MARINE SYSTEMS TEST PROJECT
TIMETABLE & KICKSTARTER 2014?
The
model(s) seen on these pages are being constructed under license for hydrodynamic
tank tests, self righting and open water sea-keeping in line with other models tested -
using radio
control initially, then switching to computer micro-controllers for
fully autonomous robotic
control and AI.
The
sensor/computer package to be used in this model as "proof of concept"
is to be revised to incorporate state of the art marine navionics for ocean
going vessels. The model will be COLREGs
compliant.
(1)
Build tank test models
(2)
Test and collate results in tank and open conditions
(3)
Make any necessary adjustments to design
(4)
Retest model in tank and open conditions
(5)
Incorporate results into final design
(6)
Begin autonomous fit-out
(7)
Autonomous systems check
(8)
Autonomous trials
(9)
Autopilot/GPS waypoint trials on pond
(10)
Full combined autonomous mission
WHY
USE ALUMINIUM ?
In
our opinion Aluminium is the best material for the construction of robust workboats. A relatively large craft built from aluminium will be lighter and stronger than if it where built from fibreglass. Marine grade aluminium has such high impact resistance, that a Buddy boat can withstand a collision that would seriously damage a fibreglass craft. Marine grade aluminium also has excellent corrosion resistance, in most cases aluminium boats will last up to 50 years in the harsh saltwater environment. Aluminium is by far the lowest maintenance material that could be used for boat manufacturing. Aluminium does not rust or rot. Residual values for aluminium boats are high - making overall cost of ownership low.
STRENGTH
OF ALUMINIUM
Aluminium has a higher yield strength than steel. It takes a force of around 30,000 psi (207MPa) to bend mild steel to the point where it won't spring back into shape when released. This is known as the 'yield strength'.
5-series Aluminium alloys will not yield until about 39,000psi (275MPa) - roughly 30% stronger than steel. A typical
fibreglass hull, by comparison, is fairly brittle and will crack before flexing significantly.
In practice this means that an aluminium boat will be able to withstand collisions that would dent the same boat made of
steel, and write off the same boat made of
GRP.
Material
|
Aluminium
|
Steel
|
Weight
|
2.65t/m3
|
7.86t/m3
|
Yield
Strength
|
275MPa
|
207MPa
|
Ultimate
Tensile Strength
|
310MPa
|
345MPa
|
Corrosion
resistance
|
Excellent
|
Poor
|
|
WEIGHT OF
ALUMINIUM
Aluminium is only around 35% of the weight of steel. This means that given a weight constraint, we can afford to use about 3 times more material in an aluminium boat than in steel - allowing us to use thicker shell plating, bulkheads, frames and decking.
A lighter vessel is easier to launch/recover by road trailer and typically only requires half the engine horsepower to match the performance of a similarly sized
GRP boat. That said, carbon
fibre is a much stronger material.
DURABILITY
OF ALUMINIUM
5083
and 5383 marine-grade aluminium alloys are preferred for marine applications because of its strength and resistance to salt-water. It has the highest strength of the non-heat treatable aluminium alloys and retains exceptional strength after welding. Marine-grade 5083 has a working life of around 100 years.
Aluminium corrodes differently to steel. Unprotected steel will rust when it comes into contact with
oxygen and water and the resulting layer of corrosion is still permeable, meaning the material can rust right through if unchecked and untreated.
When aluminium corrodes the resulting layer of oxidation is air-tight and rock hard, keeping the material underneath
highly protected. Even scrapes and scratches will form their own protective coat over time. This is why
most alloy boats are not painted, and the majority of operators choose not to
anti-foul - further reducing maintenance costs and environmental
impact.
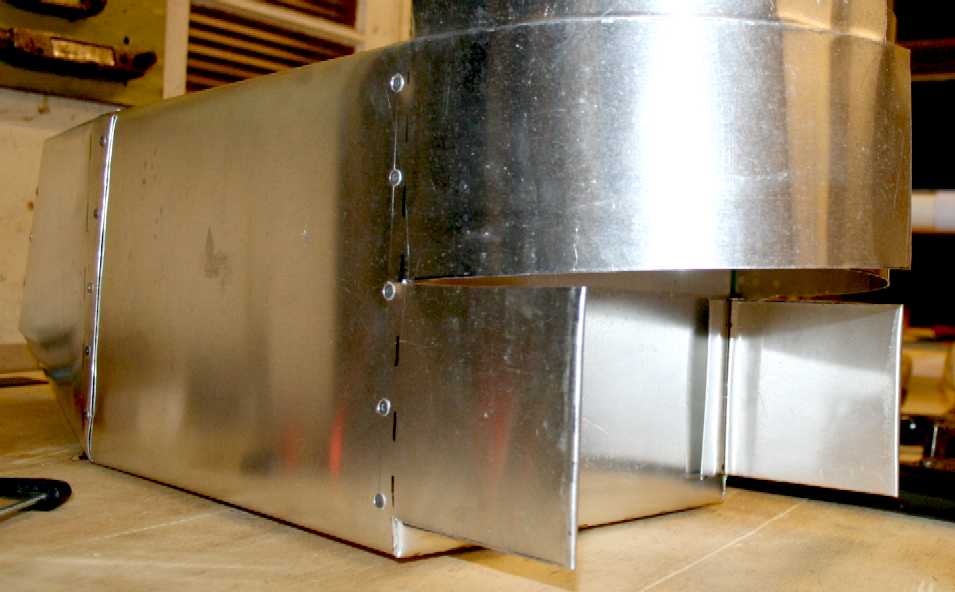
SEAVAX
- The making of a small proof of concept workboat in aluminium sheet.
COST
OF ALUMINIUM
The initial outlay for an aluminium craft may be higher than that for a comparable steel or fibreglass build,
but that cost will quickly be recouped:
>
Hull maintenance typically amounts to a cursory visual inspection, regular cleaning and replacement of the sacrificial anodes. This should keep the hull looking like new in 10 years time.
>
Aluminium does not need any protective painting, and the majority of operators do not apply anti-foul - this saves the cost of regular rubbing down and re-painting. The money you will have saved having your steel boat repainted will more than pay back the difference.
>
Being lighter, aluminium vessels can operate with smaller engines than similar steel and fireglass builds, offering a saving on the initial cost of an engine and superior fuel
economy - a real bonus with a solar powered ship.
>
Aluminium vessels have a high resale value thanks to the long life and high durability of the material.
At the end of a vessel's working life, the aluminium can be sold for
recycling, also reducing the impact of natural resources.
ADAPTABILITY
Aluminium vessels lend themselves to customization like steel. Unlike fibreglass (which would require a mould for every permutation of the design), we can start with a basic hull and easily change the length, beam, cabin layout, deck configuration, etc. to suit
the intended use. We use a CAD system that allows us to quickly modify hull
designs to suit a particular needs and keep costs down.
ALUMINUM
ALLOYS
1100
- This low-strength alloy has excellent
corrosion-resistance, has satisfactory anodizing and
conversion coating finishing characteristics, and is
unmatched by any other commercial aluminum alloy in
workability. It lends itself readily to welding, brazing
and soldering, but tends toward gumminess when machined.
Typical end uses are spun holloware, fin stock, chemical
storage, and processing equipment, kitchen utensil items,
and general sheet metal work.
3003
- About 20% higher in strength than 1100 but retaining an
excellent workability rating. May show some slight
discoloration when anodized, but reacts well to mechanical
and organic finishings. Is easily welded and brazed, but
soldering is limited to the torch method. Like 1100, tends
to be gummy when machined, but will perform somewhat
satisfactorily in the higher tempers withthe proper set-up
and maximum speeds. Typical end uses include food and
chemical handling equipment, appliance components,
truck/trailer roofing, heat exchangers, pipe jacketing and
lawn furniture components.
5005
- Comparible to 3003 in strength and close to it in
formability, but this alloy has superior finishing
characteristics making it much better for anodizing.
Excellent corrosion-resistance and weldability, but would
rate somewhat below 1100 and 3003 for brazing and
soldering, and it is not the alloy one would choose for
machinability. Typical end uses are decorative trim,
utensils, mobile home siding and reflectors.
5052
- For many years, until the advent of 5083 and 5086, this
alloy was the highest strength non-heat-treatable alloy
commercially available. Although easily welded, it is not
recommended for brazing and soldering applications.
Excellent corrosion-resistance, particularly in marine
applications, and adapts to most mechanical and finishing
processes although the heavier anodic fi lms may take on a
yellowish cast. Fair machining with proper set-up. Typical
end uses include fuel tanks, truck-trailer side panels,
small boat hulls, truck cabs, bumpers, storage tanks and
pressure vessels.
5083
- With excellent corrosion-resistance and weldability,
together with high strength, this alloy was designed for
welded structures requiring maximum joint strength and
efficiency. Can be anodized for increased
corrosion-resistance, but does not lend itself to
decorative applications. Not meant to be a machining
alloy, but can be machined fairly well with proper
preperations. because of its relatively high magnesium
content, the workability rating would be only fair.
Typical end uses are large marine craft, containers,
railroad cars, structurals and elevator cars.
|
5086
- Has excellent corrosion-resistance and weldability. Can
be anodized for increased corrosion-resistance, but does
not lend itself to decorative applications. Not meant to
be a machining alloy, but can be machined fairly well with
proper applications. Because of its relatively high
magnesium content, the workability rating would be only
fair. Typical end uses are marine craft, containers,
railroad cars, structurals and elevator cars.
5383
- 5383 alloy offers a 15% higher welded strength than
standard 5083 and may be used wherever a stronger welded
aluminum structure is desired, from hulls to
superstructures. Marine structures benefit from the
excellent corrosion-resistance offered by 5383. Smaller
boats (< 168 ft) benefit from improved scantlings,
which translate into structural weight savings on patrol
craft, increased strength on work boats and added interior
space in luxury yachts. Larger vessels (> 168ft )
profit from the increased strength and improved fatigue
behavior of 5383 alloy. Cruise ship superstructures can be
lightened further while improving stability and not
compromising strength or corrosion-resistance.
5456
- Highest in strength of the commercially available
non-heat-treatable alloys with excellent
corrosion-resistance. Only fair workability and
machinability, but excellent weldability. Not recommended
for brazing or soldering. Typical end uses are
high-strength welded structures, marine components,
pressure vessels and storage tanks.
6061
- Very good corrosion-resistance and finishability plus
excellent weldability and a strength level approximating
that of mild steel, this is a popular general-purpose
alloy. Machinability is good and, in the annealed state,
its workability carries a high rating, staying at the
"good" level if heat-treated without aging.
Typical end uses are aircraft landing mats, large and
small marine vessels, structural architectural parts,
storage tanks and highway signs.
6063
- A heat-treatable alloy developed exclusively for the
extrusion industry and the most important alloy in the
magnesium silicide group. Its as-extruded finish is quite
good making it satisfactory for many applications without
any additional work. Lends itself to comparatively
intricate sections making it the leading architectural
extrusion alloy. Also finds use in some decorative
applications, furniture tubing and ladder parts.
|
ALUMINUM
TEMPERS
"H"
temper-non-heat-treatable alloys / strain-hardened
H14
- Strain hardened (cold worked) without thermal treatment
and 1/2 hard.
H22
- Strain hardened and partially annealed, 1/4 hard.
H32
- Strain hardened and stabilized by low temperature
heating, 1/4 hard.
H34
- Strain hardened and stabilized by low temperature
heating, 1/2 hard.
|
H111
- Applies to products which are strain-hardened less than
the amount required for a controlled H11 temper.
H112
- Applies to products which acquire some temper from
shaping processes not having special control over the
amount of strain-hardening or thermal treatment, but for
which there are mechanical property limits
H116
- Applies to products manufactured from alloys in the 5xxx
series, for which the magnesium content is 3% nominal or
more. Products are normally strain hardened at the last
operation to specified stable tensile property limits and
meet specified levels of corrosion-resistance in
accelerated type corrosion tests. They are suitable for
continuous service at temperatures no greater than 150°F
(66°C). Corrosion tests include inter-granular and
exfoliation.
|
"T"
temper-heat-treatable-alloys / thermally treated
T6
- Solution heat-treated and artificially aged. A stable
temper.
T52
- Stress-relieved by compressing. Applies to products
which are stress-relieved by compressing after solution
heat-treatment, to produce a permanent set of 1 to 5
percent.
|
T651
- Solution heat treated, stress-relieved by stretching and
artificially aged. Equivalent to T6 and applies to plate
and rolled bar except 2219
T6511
- Solution heat treated, stress-relieved by stretching and
artificially aged with minor straightening. Equivalent to
T6 and applies to extruded rod, bar and shapes except
2024.
|
|

SEAWORK
2013 - At a time when some trade exhibitions seem to struggling, the busy gangways and strong visitor numbers to the stands at Seawork mark a pleasant departure from what has, all too often, become the norm at other events, according to
Aalco.
“Aalco Metals had a very positive experience at Seawork 2013,” reports Sales Development Director, Clive Bush. “The organisers have got it right; they put on the exhibition and do a first class job delivering the right audience. Of course, it is the exhibitors’ job to provide interesting and eye-catching displays, but past experience has shown that our investment in this particular event pays dividends.
“In addition to key UK customers, we noted a significant number of visitors from overseas which is very encouraging”
Seawork 2013 marked the fifth successive year that Aalco Metals has taken part and the company has already re-booked for next year.
More information at www.aalco.co.uk
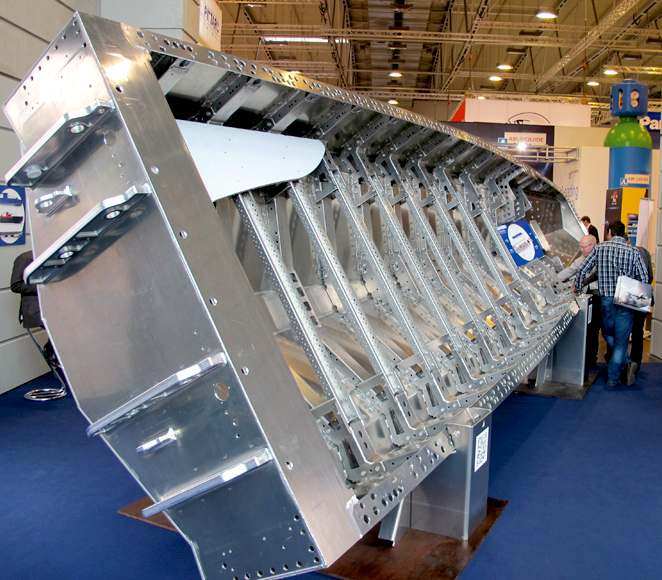
30
JAN 2015 - A German company has developed a new approach to building workboats. Instead of doing the whole of the construction in a boat yard,
Ophardt Maritim builds a range of hulls in aluminium and supplies these to owners or other shipyards for completion and fitting out.
The Opship hulls are supplied as the basic open hull, what the company calls a Boat Chassis, which gives the recipients a proven design on which to develop their own ideas for the completed vessel.
The aluminium hulls are designed in three sizes and they are all based on a unique hull design that features a moderate vee hull with wide chines for easy planing. There is a deep narrow forefoot to improve the low speed handling and a flare in the bow to provide a dry ride.
The hulls are primarily designed to accommodate outboard power with up to triple 300 hp outboards on the largest of the hulls to give high speeds. To fit these power units a bolt-on module is attached to the transom. Fuel tanks can be specified if required. Alternatively the hulls can be specified for electric propulsion using the range of Deep Blue 80 electric outboards produced by Torqeedo and with a battery pack to offer range of over 50 miles at low speeds but with the larger electric outboards, a speed of 12 knots can be achieved but with a more limited range.
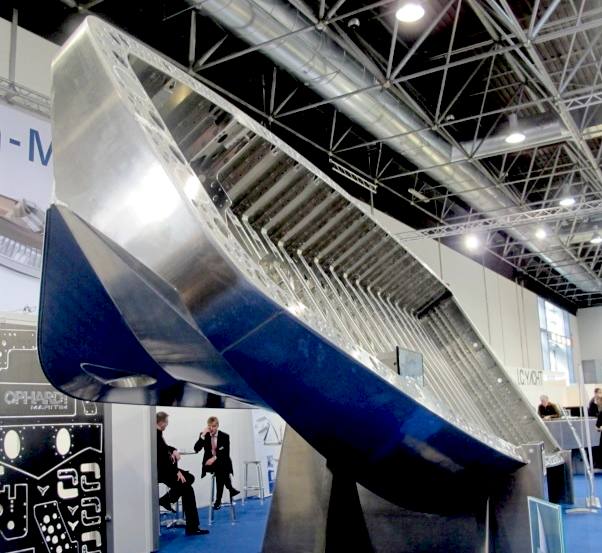
The aluminium hulls are fully welded using 8 mm plating and fitted with closely spaced transverse framing. This framing is both welded and glued in place, the glue creating a form of insulation that is designed to reduce the sound. An interior deck can be supplied over the frames or these can be left exposed for the final builder to complete as required.
The concept of the hulls developed by Ophardt Maritim is to offer an advanced and tried and tested hull concept at an attractive price. These hulls are designed to meet the demands for a wide variety of workboat roles from fast patrol boats to rugged harbour workboats. They are currently produced in sizes from 8 metres up to 12 metres and one of the main advantages is the quick delivery time. Also by focussing on just producing hulls in aluminium Ophart is able to invest in advanced construction techniques.
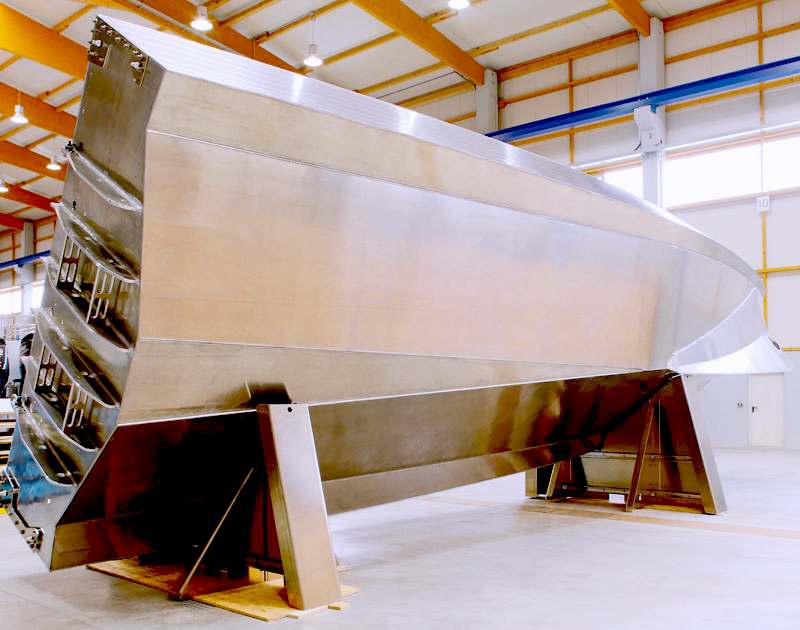
CONTACTS
- Ophardt R + D GmbH + Co. KG • Hafenstraße 69 • D-47119 Duisburg. Telefon: +49 203 - 500 322 0.
Fax: +49 203 - 500 322 51. E-Mail: info@ophardt-maritim.de
BLUEFISH
DEVELOPMENT PROJECT INDEX A-Z
GENERAL
LINKS
Maritime
Journal a new approach to aluminium workboat building
Ophardt-Maritim
http://www.ophardt-maritim.de/startseite/
http://www.maritimejournal.com/news101/vessel-build-and-maintenance/ship-and-boatbuilding/a-new-approach-to-workboat-building
Bluebird
Marine Systems Ltd
Solar
House, BN27 1RF, United Kingdom
+
44 (0) 1323 831727 +44
(0) 7842 607865
INTERESTING
EARLY
DEVELOPMENT TEST MODELS - LINKS
Blackcurrant
1 | Blackcurrant
2 | Catamaran
Hull Design
Drag
| SWASH |
SWATH
| Trimaran
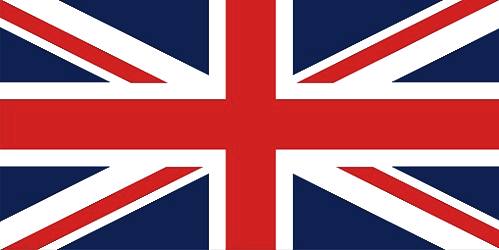
|